|
Post by Robert on Nov 29, 2013 14:06:11 GMT -8
Hey there. I am ready to start the casting adventure. Could you please share some of your experience. I will go for the mould that has been published by Peter, since his advices tell me that it is better for the cast and to get the air out...
i just have a technical question. If i pour the cement to one part of the mold, then i will have to cover the other one, and attach it with some screws?
And how the concrete which will be to much will get out from the mold? And also how the air will get out if it will become solid kind of a box? Should i make some holes in a side of one mold?
thanx for the advice.
|
|
|
Post by peterberg on Nov 30, 2013 1:38:13 GMT -8
Robert, I'm not sure I do understand what you mean. Anyway, casting the firebox and riser half is done with one side open. In effect, a box with no lid on it. The riser is thought to have a fill piece, when the complete mode is filled up to a certain level you have to mount that using screws or other means and pour the rest. Could you post a picture so we could see what the problem could be?
|
|
|
Post by Robert on Nov 30, 2013 13:58:47 GMT -8
I am sorry. My English is not so good, sometimes i have problems with expressings thought and ideas. But pictures are very helpfull, so i will try using them to describe what i mean. My questions might be very simple for those who did casting before and they may seem to be an obvious thing. But lets try... I want to use the mold design that was published by Peter which consist of two pieces. 1. The first piece i just put on the table. This is simple:)  2. Then i pour estimated amount of the concrete (with just a little bit more, to be sure it will be enough)  3. And now i place the other part on top...  and now i have few question about this stage: - how i will get rid of an excess cement? should i make some wholes in the top of the second piece? - if there will be no problem to get out of the air bubbles from the casting if the whole thing will be "closed" in the box? Sorry for asking such a basic stuff but i am learning and i really appreciated this place and patient teachers like all of you here:) robert
|
|
|
Post by peterberg on Nov 30, 2013 14:50:06 GMT -8
Robert, Leave the lid out entirely. Your drawing do contain two green pieces. One is the right hand side bottom fill part. Glue or screw that to the side of the box. Divide the other piece in three separate parts. Fix the rear fill part of the riser to the side of the box. Leave the middle part out, the third part could be mounted as a bridge. The trick is to fix the bridge to the box, by means of a piece of plywood which can be screwed to the edges of the box. This way, you should be able to pour the whole piece without a lid at all. You do need a vibrating table of some sort. When the refractory is properly vibrated and is dry enough, there shouldn't a problem with filling one part higher than the other. In order to avoid difficulties however, you could use a separate block during pouring to restrict the level in the riser part.  This drawing is not to scale or whatever, just to give you the general idea.
|
|
|
Post by Robert on Nov 30, 2013 15:56:24 GMT -8
Thanx for the idea. I am just wondering if it wil be possible to use this form later on? I would wish to have a form that i can use for making few castings.
|
|
morticcio
Full Member
 
"The problem with internet quotes is that you can't always depend on their accuracy" - Aristotle
Posts: 371
|
Post by morticcio on Dec 2, 2013 9:55:47 GMT -8
Thanx for the idea. I am just wondering if it wil be possible to use this form later on? I would wish to have a form that i can use for making few castings. I've used my moulds to make 5 casts so far - 3 were test ones using standard concrete, one using insulating castable and last one using 1600C castable. Still got a few more casts in them yet I hope!
|
|
morticcio
Full Member
 
"The problem with internet quotes is that you can't always depend on their accuracy" - Aristotle
Posts: 371
|
Post by morticcio on Dec 10, 2013 16:13:45 GMT -8
Been making the frame and door for the stove with a friend and am now building the test stove in the shed before it goes in the house so here are some photos. The stove will sit on a wooden floor hence the frame and insulation. Made from pallet racking. Clearance is 8 inches (200mm) 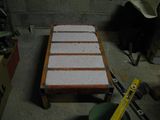 Door... decided not to have a window and has rotary air control. 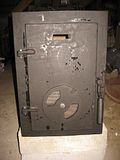 Door and frame. Made from 'scrap' checkerplate. Thank goodness for plasma cutters! 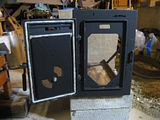 Base sits on 3mm ceramic paper and is laid dry using 64mm fire brick. Remainder will be using 76mm on edge using clay slip. I haven't included a clean out as this will be taken apart after testing. Space on front is for a shelf to load wood/ash removal. 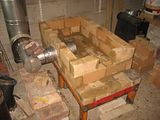
|
|
morticcio
Full Member
 
"The problem with internet quotes is that you can't always depend on their accuracy" - Aristotle
Posts: 371
|
Post by morticcio on Dec 10, 2013 16:37:09 GMT -8
Piers to support the door frame assembly. Maybe I should round the corners off to help airflow? The inner dimensions of the bell are approx. 33" x 18.5" (850mm x 450mm). Height will be 6' (1800mm) 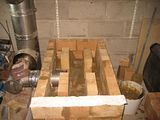 Door frame assembly with 25mm vermiculite board for the stove to sit on. Big thanks to Andy for making the door & frame! 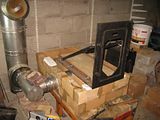 Another view of frame assembly. Studs are for clamping the stove together and securing the superwool which will be wrapped round it. 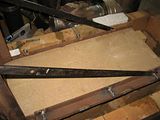 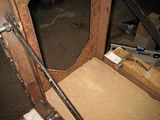 Batch box halves on frame assembly with P-channel poking through. This needs to be trimmed to fit. 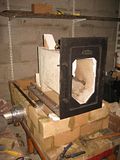 Spare bits of insulated firebrick cut off to 45 degrees to insulate the V on each side of firebox. These still need to be trimmed to fit 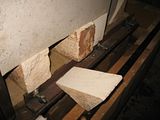 And the same for the back of the riser. Again they need to be trimmed to enable superwool blanket to fit snugly. Trying to insulate the batch box as much as possible! 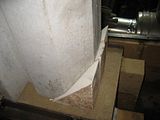
|
|
|
Post by Robert on Dec 12, 2013 8:45:44 GMT -8
Great Job... and give a hug to Andy from me... wonderfull doors... kind of heavy but well... the doooors of perception  i am still looking for someone who will make one for my stove 
|
|
morticcio
Full Member
 
"The problem with internet quotes is that you can't always depend on their accuracy" - Aristotle
Posts: 371
|
Post by morticcio on Dec 12, 2013 17:01:36 GMT -8
|
|
|
Post by Robert on Dec 15, 2013 9:01:01 GMT -8
great job!!! i have two questions. 1. what about this steel frame kind of thing. The one that binds the core together, and the frame of the doors are connected to it. I am wonder how it will react with temperature? will it not bend? You think there will be no problems with doors being "pushed" out? 2. What is that dark piece over the door frame... its some kind of a support for the next layer of bricks as i suppose... what is this made from? 3. what is teh ISA of the bell? 4. You would not like to place the oven there? and yes... i am jelaous, waiting for the day when i build my bell rocket 
|
|
|
Post by matthewwalker on Dec 15, 2013 9:38:40 GMT -8
That's a heck of a nice stove Morticcio! Can't wait to see it all done and in the house. I love the hardware, very cool.
|
|
morticcio
Full Member
 
"The problem with internet quotes is that you can't always depend on their accuracy" - Aristotle
Posts: 371
|
Post by morticcio on Dec 15, 2013 11:03:11 GMT -8
Robert, thanks for comments. Here's some answers Q1. what about this steel frame kind of thing. The one that binds the core together, and the frame of the doors are connected to it. I am wonder how it will react with temperature? will it not bend? You think there will be no problems with doors being "pushed" out? A1. The steel we used for the door is heavy, heavier than it needs to be, but was scrap hanging around in the shed for past 10 years. We welded 40mm angle iron to (hopefully) prevent any warping. I have allowed for expansion and used superwool/ceramic paper as gaskets where possible. Will be firing the stove daily over the next week to check for any stress/cracks etc. The steel frame & perlite is great too - the underside is cool to touch even when the stove is an inferno.
Q2. What is that dark piece over the door frame... its some kind of a support for the next layer of bricks as i suppose... what is this made from? A2. Its Welsh slate, approx. 70mm thick. It was left over from the window cills (or sill) when we did the barn up 12 years ago. I had a 450mm firebrick I could have used but found this piece of slate and thought it fitted it well with the stove and door. The shelf below the door is the same material.
Q3. What is the ISA of the bell? A3. Approx. 5m² as I stacked some additional firebrick behind the riser.
Q4. You would not like to place the oven there? A4. I have thought about an oven so there might be one in final installation! We did make pizza in the stove last night :-)
I couldn't wait to build my own bell stove either! It has taken over 9 months to get to this stage. I must've build this stove in my head a thousand times. It was great to eventually light it for real :-)
Many thanks to everyone on here for their plans, ideas & inspiration. And a massive thanks to Andy for helping with the moulds, frame & door.
Matt Much appreciated. The door works great. I don't really miss the window - you know by the noise it makes if it is running well and you can see the flames through the grill if you really need to! Handle stays cool to touch which I wasn't expecting. Also, a clean white firebox must be a good sign, but would love to test combustion efficiency etc so if anyone near Bristol has a flue gas analyser please get in touch!
One modification - when the P-channel slider was closed there was no noticeable difference in the rocket roar so I added a strip of rope to seal between the top of the firebox and the P-channel. It seems to have done the trick - now when the slider is closed you can hear the rocket roar lower significantly. This also remains much cooler than the rest of the door.
|
|
radek
Junior Member

Posts: 94
|
Post by radek on Dec 15, 2013 11:48:09 GMT -8
those are one beautiful stove Morticio,clean design.One thing ill sugest for the finnal plaster and thats to add some kind of mesh in to the plaster.Wire mesh or special mesh for heaters.Because its single skin heater made out of fire bricks it will be expanding and contracting quite a bit so ill for sure add the mesh it there and prepare my self for tiny cracks in plaster.So again realy nice heater.
|
|
|
Post by satamax on Dec 15, 2013 11:54:02 GMT -8
My opinion is leave the bricks showing. Bricks look cool to me!
|
|