|
Post by smarty on Mar 17, 2013 9:40:18 GMT -8
By the way - anyone know what volume of refractory you end up with from a 25 kg bag? Kevin You get through two 25kg bags casting this mould. The chamfer you mention is what they call a 'draw' in sand casting where the pattern needs to be drawn out of the delicate casting sand mould. You are also right about the radius on the right angles where the corner is apt to get trapped. A bead of silicone smoothed with the finger does this quite well on internal corners.
|
|
morticcio
Full Member
 
"The problem with internet quotes is that you can't always depend on their accuracy" - Aristotle
Posts: 371
|
Post by morticcio on Mar 17, 2013 14:04:36 GMT -8
By the way - anyone know what volume of refractory you end up with from a 25 kg bag? Kevin You get through two 25kg bags casting this mould. Using a SketchUp volume add-in, each side of the mould is approx 11.5 litres (706 cu in or 0.41 cu ft)
|
|
|
Post by matthewwalker on Mar 17, 2013 14:20:12 GMT -8
When choosing your castable, the spec sheet should show density. Using the volume of your mold and the density of the product you can figure out how much you'll need. An insulating refractory might only require about 30lbs to fill the above mold example, while a dense refractory may need 70lbs to fill the same mold.
|
|
|
Post by phlogiston on Mar 17, 2013 20:33:25 GMT -8
You get through two 25kg bags casting this mould. Thanks Smarty, agree a draw is important and needed to release casting easier but not quite what I meant. In the mould the fillet at the base stops short of, and parallel to the wall/base of the riser and this space will form the leg of the casting, same at the front. if the fillet was angled to 45 deg it would make the leg thicker not just a couple of deg to aid removal. I mean radius the external corners on the mould which will translate into an internal radius on the casting. Having a sharp 90 deg gives a crack somewhere to start. Using a SketchUp volume add-in, each side of the mould is approx 11.5 litres (706 cu in or 0.41 cu ft) Must get using this Sketchup thanks Morticcio. When choosing your castable, the spec sheet should show density. Using the volume of your mold and the density of the product you can figure out how much you'll need... Cheers Matthew the product available to me is 3mm grain size, 1600°C and €35/25kg bag but the guy who sells it doesn't have a clue about how much cast volume a bag would produce. I asked him for a product spec sheet and he pointed to the phone number on the bag  I'll call the manufacturer next week and hopefully get some info, don't want to buy too much but also don't want to have too little.
|
|
|
Post by smarty on Mar 18, 2013 0:31:20 GMT -8
I think I follow you now. yes the bit of the mould that is triangular in shape that goes in between the legs and forms the external thickness of the sloping floor. Yes you are quite right I looked on the one I cast the other day and that is what I did kind of. It's not quite as much as 45 degrees more like twenty or so but way more than the one or two degrees of a draw.
As I said to morticcio someone told me that old washing machine motors make good vibrating motors with a cam attached if that was something that anyone was scratching their head about.
|
|
|
Post by greenjeans on Mar 20, 2013 17:22:27 GMT -8
Mattew Walker, did you do a video of a casting on youtube under broaudio, please respond. greenjeans
|
|
|
Post by matthewwalker on Mar 20, 2013 17:38:09 GMT -8
|
|
morticcio
Full Member
 
"The problem with internet quotes is that you can't always depend on their accuracy" - Aristotle
Posts: 371
|
Post by morticcio on May 6, 2013 14:43:47 GMT -8
As you can see from the photos I've not quite perfected casting & vibrating the mould but have eventually got my batch box going. Modified the mould slightly after doing some initial casts on the batch box and riser using standard concrete mix, and have used 1300C insulating castable for this test piece. The vibrating table didn't quite get all the air pockets out - has anyone tried using a 25mm/1" vibrating poker? After a number of small fires to dry it out it I tried a test run. Once the rocket noise started there was no stopping it. I'd gone indoors to get a camera to come back and find that it was now over 1000 deg C... this is even without the two halves sealed completely and the riser fully insulated. I was half exxpecting it to crack apart but it hasn't so far! Here are some photos from a burn earlier today using 5kg of wood at 12-15% moisture content. Start to finish was 1 hour with embers at 50 minutes. Front view - I'd weighed out 6.5kg and checked moisture content. Rear view - the two halves are not sealed. I'll need to get some clay slip! Flue is 7" insulated Looking into batch box Inside batch box - clean from previous fire! Lighting method Makeshift door Embers afer 50 minutes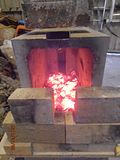 Here is some video footage taken yesterday:
|
|
|
Post by bernardbon on May 6, 2013 15:54:41 GMT -8
Nice job !
Have photos of the cast?
|
|
|
Post by bernardbon on May 7, 2013 5:17:39 GMT -8
Is it easier to make two half-shell for firebox + two half shell to the second chamber? Molds easier to build and easier to pour concrete evenly?
Bernard
|
|
morticcio
Full Member
 
"The problem with internet quotes is that you can't always depend on their accuracy" - Aristotle
Posts: 371
|
Post by morticcio on May 7, 2013 6:28:44 GMT -8
Is it easier to make two half-shell for firebox + two half shell to the second chamber? Molds easier to build and easier to pour concrete evenly? Bernard Yes it would but you'd need to ensure they join together and don't get knocked apart. Saying that I'm hoping to add a 200mm/8" extension on the front so it will take 500mm/18" lengths of wood. The riser in the picture is a test cast using normal concrete. The batch box is using the insulative castable. 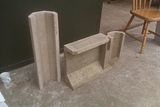 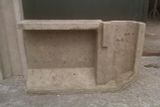
|
|
|
Post by peterberg on May 7, 2013 8:39:10 GMT -8
Very glad to see someone is using the right proportions and some tips and tricks. With commendable results, I like that, a lot. Thank you, Morti. ;D
|
|
|
Post by vuurenvlam on Jun 16, 2013 14:37:20 GMT -8
I also want to attempt a casting of a mould similar to this, but don't have much woodworking tools which makes cutting long pieces of wood at angles very tricky. I've been thinking of ways to simplify the mould. I want to split the mould into two, the fuel box and the heat riser. One idea I had to simplify was to use a 6" PVC pipe (yellow) mounted in a box:  The green is the inlet into the heat riser, the other side of the mould would have the green piece removed. To keep it really simple, I could leave out the red inserts (at the expense of needing more refractory). It doesn't include the slant found at the bottom of the original heat riser, but my idea is to make this as a loose piece to insert later. Another idea would be to mount two PVC pipe halves (a 6" and a 8") onto each other, but I'm not sure if it would be easy enough to poor the refractory into if this mould is laid horizontally. If put vertically it could be rammed in, but from what I've heard this will make it too hard to release air bubbles. Any feedback or further ideas would be appreciated. @karl Could you expand on your idea below? For small lots or to achieve exceptional properties, I would only build the inner mould and form a shell on it. No vibration plate required, therefore no separation. This approach is much simpler to realize and gives much more freedom. Allows to build the shell with several layers of different properties. ... The industry offers fire resistant materials which would allow to use laminate techniques. Would this technique require special materials for 'laminate techniques' or would the usual castable refractory do? How would you build onto the mould, similar to plastering a wall? Thanks!
|
|
Deleted
Deleted Member
Posts: 0
|
Post by Deleted on Jun 17, 2013 4:37:57 GMT -8
@karl Could you expand on your idea below? For small lots or to achieve exceptional properties, I would only build the inner mould and form a shell on it. No vibration plate required, therefore no separation. This approach is much simpler to realize and gives much more freedom. Allows to build the shell with several layers of different properties. ... The industry offers fire resistant materials which would allow to use laminate techniques. Would this technique require special materials for 'laminate techniques' or would the usual castable refractory do? How would you build onto the mould, similar to plastering a wall? Aside of castables the industry is offering plastic moldables, ramming mixes and moldable sheets. vitcas.com/plastic-mouldable-rams-refractorieswww.zrci.com/a.htmPeople keen to experiment may try own mixtures (worked well for me). The final strength will be lowered with high water content, thus plastering techniques may not work out well, especialy with self made mixtures. The mouldables could be formed to slabs and then pressed against a surface. Moldable sheets or blankets are similar to plaster bondages and could easily be made by oneself. Inner forms could be cut from foam boards and glued together. Does not need sophisticated tools or skills.
|
|
|
Post by vuurenvlam on Jun 21, 2013 14:52:06 GMT -8
Thanks karl, I've contacted some local refractory companies but they don't seem to stock similar products here. I think I'll go for a mould from wood/foam boards.
|
|