Deleted
Deleted Member
Posts: 0
|
Post by Deleted on Jan 17, 2014 7:27:53 GMT -8
Sorry, need better glases
|
|
|
Post by pyrophile on Jan 21, 2014 14:24:49 GMT -8
Doggy Could you please put a drawing because I don't really understand what you mean.
|
|
|
Post by pinhead on Oct 8, 2014 6:38:00 GMT -8
I can't seem to find any updates to this project. Has there been any further development? Are the dimensions pretty well spot on? If so I'll add the calculations to the Batch Box Spreadsheet.
|
|
|
Post by peterberg on Oct 13, 2014 0:50:12 GMT -8
I can't seem to find any updates to this project. Has there been any further development? Are the dimensions pretty well spot on? If so I'll add the calculations to the Batch Box Spreadsheet. This project is still going on, Sjang has been using it in a couple of customer's stoves. Regretfully, there hasn't been done extensive testing using a gas analizer. State of affairs at the moment: Sjang and myself made an appointment for coming Wednesday in order to put one of those stoves to the test. The plan is to do three full runs on a new build, not dried out yet. I'll do my best to get Sjang's consent to publish the results. Hopefully we'll aquire also firm figures of the duct sizes and placement.
|
|
|
Post by peterberg on Oct 17, 2014 11:26:26 GMT -8
The promised test session has been done, the results are very nice. We tried to provoke the stove into throwing the CO through the roof but it refused to do so. The usual tricks to let things go wrong did't work with this modification. I've got two diagrams to show, the first is a cold start, a refill halfway and some tuning of the primary air. Up to the point that the flames in the firebox became very lazy and the afterburner still roared at the same time. 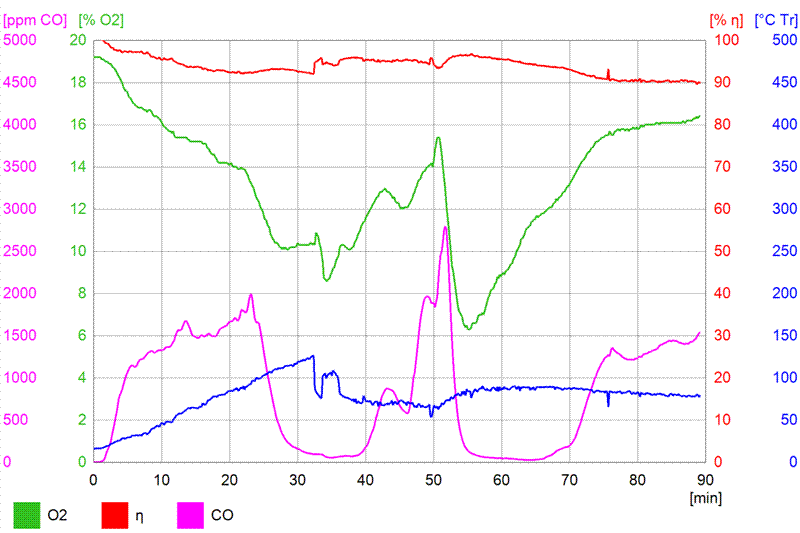 Average numbers of the first run: O2 13.2 %, eff. 94.0 %, CO 852 ppm, end temp 76.8 C. The second one is a refill on glowing coals. Short pieces of very dry beech stacked up against the back wall in such a way that the port was nearly entirely blocked. In my experience, in such a situation there's no flame in the riser and fresh fuel is off gassing like crazy, this should cause the CO to peak very high. OK, the CO went up, but not very high and as soon as the afterburner roar started everything went back to results very similar to the large batchbox at permies. 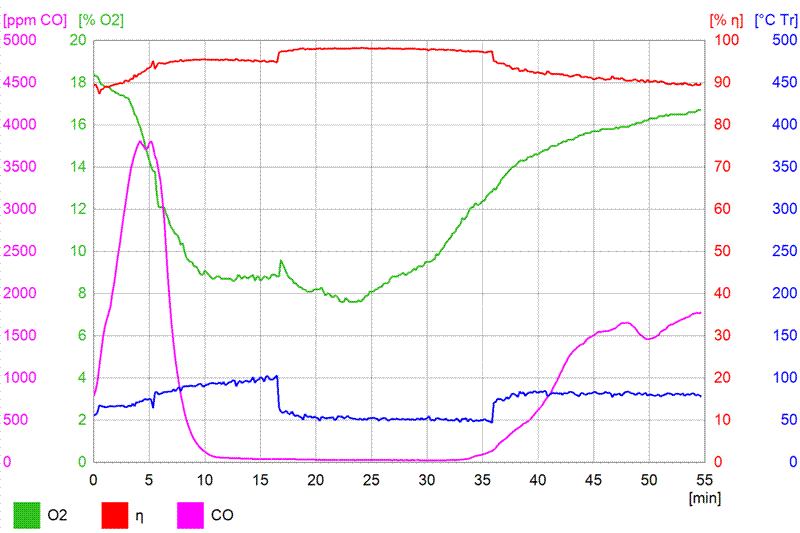 Average numbers of the second run: O2 12.2 %, eff. 94.4 %, CO 820 ppm, end temp 71.7 C. The low stack temp seems odd, this is due to a bypass which happened to be open in the first run and partly closed in the second. The stove itself is an 18 cm system, just a tad over 7", serving a bell and a short bench. Conclusion: this modification does work, the stove runs much more stable with a nice low CO line. The O2 is still a bit high but testing a commercial stove which isn't completely dry yet has to be done carefully. We've made plans to do it again some time in november and drive it a bit harder using a full load.
|
|
|
Post by pinhead on Oct 20, 2014 5:06:06 GMT -8
Were you using the dimensions as outlined in the original post of this thread?
|
|
|
Post by peterberg on Oct 20, 2014 6:06:43 GMT -8
No, that's not the case. Built as a 180 mm system the secondary air was exactly 10% of riser csa. Divided into two slits of 250 by 5 mm in the portal sides. Those tubes were 40 by 50 mm, 3.6 by 4.6 mm inside which gives a better ratio between slit and duct. In fact, the tube csa is 130% as compared to the slit. There are strong indications this tube should be even wider than that in order to achieve best performance.
At the same time the primary air is smaller, hard to say exactly but somewhere between 8% and 9% of riser csa. Flames inside the firebox were very lazy but still raging as always in the riser. It seems odd, but it works flawlessly.
As it stands at the moment: Applied to a 150 mm system (6"). Gate is 55 by 230 mm. S-portal tubes: 40 by 40 mm outside, 36 by 36 mm inside. Slit in the tube: 220 by 4 mm, start 20 mm from the bottom.
Applied to a 180 mm system (+/- 7"). Gate is 65 by 285 mm. S-portal tubes: 40 by 50 mm outside, 36 by 46 mm inside. Slit in the tube: 250 by 5 mm, start 20 mm from the bottom.
This is by no means a final conclusion, merely the state of affairs at this time.
|
|
morticcio
Full Member
 
"The problem with internet quotes is that you can't always depend on their accuracy" - Aristotle
Posts: 371
|
Post by morticcio on Oct 20, 2014 10:14:58 GMT -8
Thanks for sharing Peter. The CO readings after the refill @ 45 min on the first graph bottom out for 15 mins or so. On the second graph, the CO readings bottom out for 25 mins. Do you think the half closed damper could have something to do with this drop? Sjang, some photos of the stove/build would be great if you have them.
|
|
|
Post by peterberg on Oct 22, 2014 0:51:54 GMT -8
On the second graph, the CO readings bottom out for 25 mins. Do you think the half closed damper could have something to do with this drop? I feel the CO hasn't anything to do with the bypass in this case. The CO went down BEFORE closing of the bypass and kept being low when opening it again.
|
|
|
Post by doggy1969bc on Oct 25, 2014 7:36:21 GMT -8
Doggy Could you please put a drawing because I don't really understand what you mean. what i mean to say is if you take the portal and put the opening of the secondary air more to the heatriser side ,almost in the heatriser
|
|
|
Post by Donkey on Oct 26, 2014 13:00:51 GMT -8
Built as a 180 mm system the secondary air was exactly 10% of riser csa. 'snip' Interesting.. These modifications are reducing the need for air by quite a bit. The old stand-by with J-tubes was 25% (1/4 system size). Correct me if I'm wrong, but I believe that the standard Batch-Box is 20% primary air and 5% secondary (P-channel) for 25% combined. Here, we're looking at combined intakes of 19% with VERY clean results. Another interesting change, (this one make a lot of sense to me) in this configuration secondary air is a larger portion of the intake(s).
|
|
|
Post by peterberg on Oct 27, 2014 0:46:04 GMT -8
Interesting.. These modifications are reducing the need for air by quite a bit. The old stand-by with J-tubes was 25% (1/4 system size). Correct me if I'm wrong, but I believe that the standard Batch-Box is 20% primary air and 5% secondary (P-channel) for 25% combined. Here, we're looking at combined intakes of 19% with VERY clean results. Another interesting change, (this one make a lot of sense to me) in this configuration secondary air is a larger portion of the intake(s). Yes, you are right, the air intake of the primary/p-channel is 25% together. Judged by the excess air numbers of this tests, the secundary air values could be smaller again, probably something like a 50/50 ratio. I've known for years that one could reach for top efficiencies when it would be possible to lower down the excess air and achieving a clean burn at the same time. Such a possibility seems to be at on the horizon now...
|
|
|
Post by Donkey on Oct 27, 2014 9:31:16 GMT -8
Umm.. It seems to me that with this design, primary air was reduced most with secondary air actually being increased. Do you think that further reductions would continue this same pattern? Or not?
I'm currently wondering if perhaps it makes MORE sense that secondary air would remain higher. Most of the fuel to be burned is gaseous, traditionally secondary air is for burning these gasses. This thought-form points towards gasification stoves and the lot for clues to questions.. Perhaps.. ??
|
|
|
Post by doug58 on Nov 4, 2014 15:40:25 GMT -8
|
|
|
Post by Robert on Nov 7, 2014 18:18:49 GMT -8
this is extremally interesting... i am wondering how will this metal behave in a stove? i like the way Joris is using ceramic P-channel... i would be much more shure for a durability of that solution... have you heard if Sjang or anyone tried the S-Channel made from firebrick?
|
|