|
Post by peterberg on Jun 14, 2019 0:03:31 GMT -8
Thank you Peter. I had calculated 77 percent of base rather than 5 percent more than port size itself. When I get the chance I am considering making the port in the side to use the top box as a cook top. Just out of curiosity. Then I will add the stumbler as well i think Having the port in the side is not tested at all, so I don't know whether it would work. Somebody else tried a 125 mm core with a cooking plate 10 cm above the end port and it worked, no problem. So I'd think that would be the safer option. I calculated the width of the end port in your system as 69 mm if I remember correctly, so 70 mm would be fine. Be careful not to make it smaller or equal as the first port, you could end up with a recalcitrant device.
|
|
|
Post by Orange on Jun 14, 2019 6:31:39 GMT -8
I've never said it required superwool. Yasin used split firebricks to shrink the space to riser proportion. At the time I didn't have splits at hand but 1" superwool did work as well. Heating up of the riser is quicker this way, CF board could be another option. Question remains whether or not the system would work properly without infill at all, this could be tested sometime. At the moment I could take the wool out but getting it in again would make a hassle of partly demantling the setup. great, thanks for the clarification. I guess that insulating the whole firebox also won't make much off a difference in regards to combustion efficiency.
|
|
|
Post by travis on Jun 14, 2019 6:59:36 GMT -8
Ok sounds good Peter! I am excited to do more building and see how things hold up this coming winter.
|
|
|
Post by peterberg on Jun 16, 2019 8:05:24 GMT -8
Eight days ago I tried the idea Helm suggested, adding air in the top of the door only. The test was done with pine lumber scraps, half a load so lots of air was allowed over the fuel. Size of the opening was 50x160 mm, quite sizeable and twice as much as what Helm suggested. It went quite good, burn was a bit sluggish. At 26 minutes I added two bigger pieces of fuel, expecting to see a rise in CO and dip in O². It was there alright, but the burn slowed down at this point until I opened the door just a crack at 34 minutes so it picked up again. 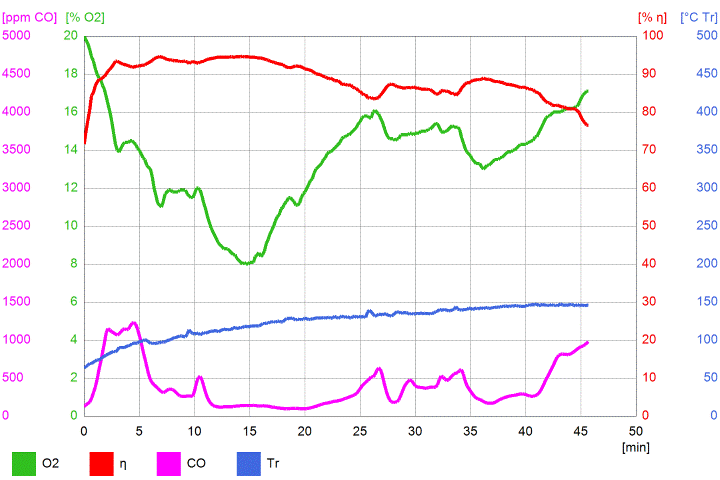 It looked promising nevertheless, so I dismantled the door frame and air frame. Cutted out the duct above the firebox door and welded one in with a sizable slit in it. Everything assembled again, taped off the slits at the sides bar a small piece at the top. So air was coming in through the vertical ducts of the air frame, open on all sides. Started a test using a full load, up the the top of the port. This test didn't went wel, I experienced great trouble trying to get it stable, opening all air inlets and closing those gradually one by one. 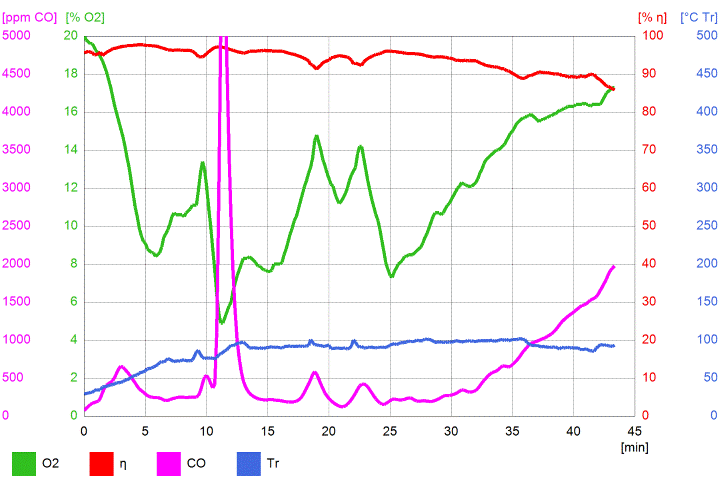 Next run I opened up part of the side air inlets since it appeared the port didn't receive enough air. In short, I tried different air inlet configurations to no avail. None of the runs seemed to reach a stable state of affairs. After some grumbling and swearing I taped all the air inlets, took out the glass of the door and mounted the screen and plate so the 50x160 mm opening was there again. Loaded the firebox full and let it warm up with open door until the stack temperature reached 100 ºC. 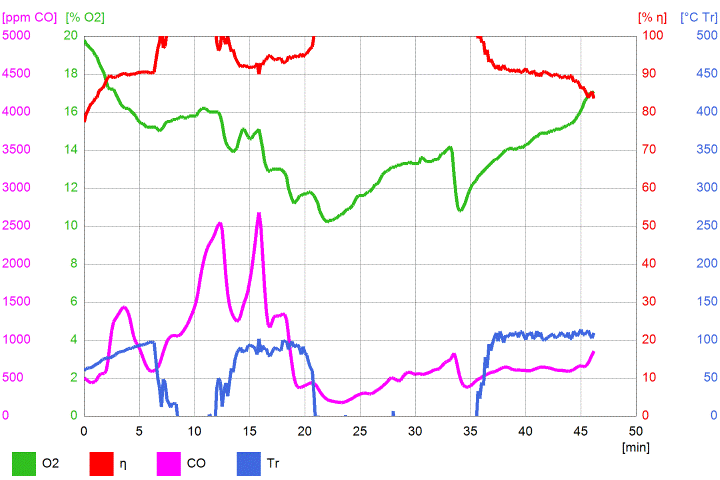 As can be seen, this wasn't a good run, at all. It did smoke a bit in the beginning, looked sluggish, the rumbling rocket sound faded and started again now and then. Not good enough for the EU norm 2022 at any rate. Please ignore the temperature and efficiency readings in the above diagram, the thermocoupler of the Testo seems to be losing now and then. So I ditched the whole of the top air idea and focused on re-introducing the floor channel combined with side air inlets. I tried several combinations but at the end a combined air inlet in the lower part of the door together with a normal sized floor channel and side slits behind the door appeared to have the best papers.
|
|
|
Post by sksshel on Jun 16, 2019 8:31:39 GMT -8
Could you also try a run with the normal size floor channel and a full screen door? You may have already tried this combination.
|
|
|
Post by peterberg on Jun 16, 2019 9:03:19 GMT -8
Could you also try a run with the normal size floor channel and a full screen door? You may have already tried this combination. Yes, I did. In that case you'd do better to leave the floor channel out entirely, it won't add anything bar complexity. There will be two separate designs of this DSR2, an open version with or without screen door and a closed version with floor channel, air inlet and glass door. Those won't be interchangeable as such, firebox of the closed version will be a bit higher because of the air inlet arrangement. The open version is the simplest to build obviously, I did that about a week ago for somebody else, meant as a core for demonstration purposes. I performed 14 recorded test runs in eight days and some unrecorded. In the mean time I rebuilt the air frame 3 or 4 times, I've lost count. My stack of decent firewood is completely gone by now, only small pine scraps is what's left.
|
|
|
Post by independentenergy on Jun 16, 2019 11:33:08 GMT -8
it seems that the all-open door does not need a second combustion air
|
|
|
Post by peterberg on Jun 16, 2019 12:30:22 GMT -8
Yes, definitely.
|
|
|
Post by wiscojames on Jun 16, 2019 14:35:31 GMT -8
Start sending Peter dry firewood!
|
|
|
Post by sksshel on Jun 17, 2019 6:36:22 GMT -8
it seems that the all-open door does not need a second combustion air With the open door version, is it ok to use my existing secondary air tube or do I need to remove it and replace it with geopolymer?
|
|
|
Post by peterberg on Jun 17, 2019 8:25:05 GMT -8
With the open door version, is it ok to use my existing secondary air tube or do I need to remove it and replace it with geopolymer? Assuming the secondary air tube is in a thrench in the firebox' floor, just take it out. It will burn out shortly because it won't be adequately cooled anymore. Just fill the trench with ashes, that's what I did at a certain stage. The effect is that the ashes will form clinkers, not what you expect of wood ashes in most circumstances. It might be that you need to plug the front of the trench with a piece of steel tube.
|
|
|
Post by peterberg on Jun 18, 2019 11:41:15 GMT -8
Last state of affairs: a floor channel of normal proportions plus long narrow gaps in the side of the air frame are definitely the best combination I have found so far. Normal proportion would be in this case a stub part of 30x30x2 mm (1.18" x 1.18" x 0.0787") combined with a feed part of twice as large. So two 30x30x2 channels side by side and cut out like the ones in the picture below would be perfect. 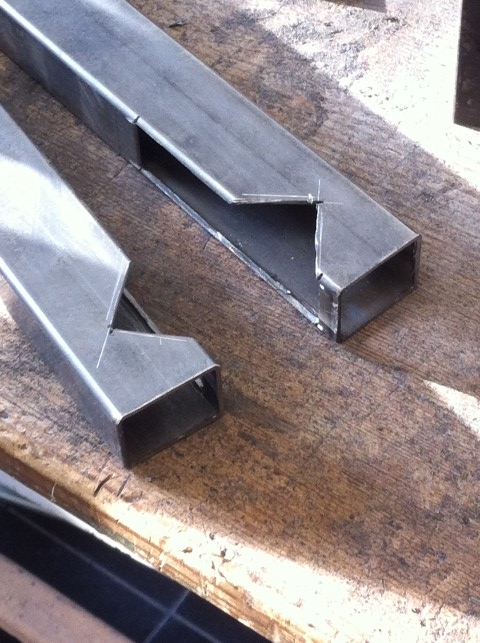 The slits in the sides of the air frame are fed through the duct of the frame itself. The door could just be bare, with the inlet in the frame underneath the door. I'll make some drawings in the coming weeks to cater for these details.
|
|
|
Post by patamos on Jun 21, 2019 10:01:54 GMT -8
Thanks for all your efforts on this Peter 
|
|
|
Post by Orange on Jun 21, 2019 12:57:19 GMT -8
yes, there should be a donation button because it's difficult to send dry wood to Holland 
|
|
|
Post by sksshel on Jul 25, 2019 9:54:31 GMT -8
Is the DSR2 RC1v8.skp the most current version of the design? Do you have an "open version" .skp?
Assuming the design is considered stable at this time, I plan to begin construction on the upgrades from my current DSR soon.
|
|