|
Post by pinhead on Oct 20, 2016 6:35:52 GMT -8
I decided to marry the girl that helped me build the Brick Body Batch Box so I'll be moving at the end of October after the wedding.  Since we're renting, I can't put a rocket stove in the house. I'm not sure if they'll let me cut a hole in the garage for a chimney, either, so our last option is to build it in the cellar which will serve as my HAM shack and electronics work area. The cellar is detached from the house, about 20 feet away. It's dark and gloomy so the concrete walls will need to be painted to make it brighter and we intend to install 12vDC lighting with battery backup so it can double as our storm shelter. We figured this would be a perfect place to experiment with various rocket and bell designs. Since the temperature already stays fairly stable at around 55°F, I won't need a high-output stove. On the other hand, it'll need enough capacity to heat up fairly quickly (since I won't light it in the mornings before work during the week) yet need enough thermal storage to heat over the weekends when I'll spend more time down there. I haven't measured the dimensions of the cellar yet, though, so I haven't yet made any dimensional drawings/plans. The cellar is pretty much air-tight other than the front door and an 8 inch vent tube in the ceiling. I suspect a 6" J would produce plenty of heat for the airtight space, though I've come to prefer the batch box design due to the size of logs I can burn. In my old shop I had a 7-inch side-riser batch box and it performs extremely well. That shop was leaky and uninsulated so I won't need near the amount of heat in this cellar as I did in my old shop. Here's my proposed design: A 6-inch batch box made of brick, wrapped with rockwool insulation with a ceramic blanket heat riser. The single brick bell will surround the entire batch box and the entire contraption will look a lot like this, with either brick or cinder block instead of tile: 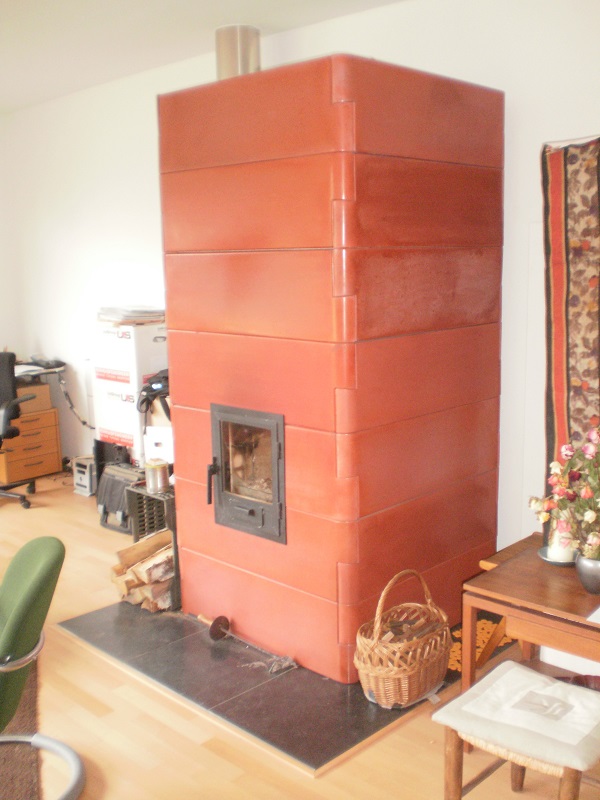 The only concern I have with this design, though, is the initial heat-up time; due to how I'll be using the cellar, the stove will need to heat up fairly quickly. I might need to use a small portion of a steel barrel at the top for quick heat while the brick/masonry serves as the thermal storage. Due to the air-tightness of the cellar and nature of the work I'll be doing in there, I intend to build a bypass in the bell for quick start-up and to reduce/eliminate smoke-back during warm-up and refilling. This is where my experience wanes, however. I intend to build a "chimney" out of brick/cinder block in a corner of the bell with a low inlet and then the bypass will be an opening further up with a steel slider to open the bypass(Thank you, vortex, for the idea). Should the bypass be at the top of the bell? Half-way down? How is the optimum location determined? Trial and error?
|
|
|
Post by satamax on Oct 20, 2016 6:48:51 GMT -8
Pinhead, make the top slab cast iron, and add a oven door un front. Make the walls thinner like two bricks on edge. ;D
|
|
|
Post by peterberg on Oct 20, 2016 7:30:50 GMT -8
I intend to build a "chimney" out of brick/cinder block in a corner of the bell with a low inlet and then the bypass will be an opening further up with a steel slider to open the bypass(Thank you, vortex, for the idea). Should the bypass be at the top of the bell? Half-way down? How is the optimum location determined? Trial and error? In my opinion,the bypass should be just above halfway up but lower than the riser top. This way, there's a very shallow bell in the top of the heater when the bypass is open. That brick upstream channel in the corner is a proven concept, the ISA of the bell stays the same this way. What you could do in order to shorten the warming up time is to build the whole thing as a single skin.
|
|
|
Post by pinhead on Oct 20, 2016 9:27:48 GMT -8
Pinhead, make the top slab cast iron, and add a oven door un front. Make the walls thinner like two bricks on edge. ;D The thought has crossed my mind. I'll have to ask Kelsi if she'd ever use an oven down there. I intend to build a "chimney" out of brick/cinder block in a corner of the bell with a low inlet and then the bypass will be an opening further up with a steel slider to open the bypass(Thank you, vortex, for the idea). Should the bypass be at the top of the bell? Half-way down? How is the optimum location determined? Trial and error? In my opinion,the bypass should be just above halfway up but lower than the riser top. This way, there's a very shallow bell in the top of the heater when the bypass is open. That brick upstream channel in the corner is a proven concept, the ISA of the bell stays the same this way. What you could do in order to shorten the warming up time is to build the whole thing as a single skin. Even if the bell extends multiple feet above the riser?
|
|
|
Post by peterberg on Oct 20, 2016 11:19:33 GMT -8
That's correct. Somehow it seems easy for the gases to turn back to its entry level in the bell. But going lower than that it looks like there's a lot of resistence which is growing when it is getting lower. At the top of the bell it is awfully hot, not good for steel objects, and down to the level of the riser is easy (for the gases).
|
|
|
Post by pinhead on Oct 20, 2016 13:02:09 GMT -8
I intend to make the exit of the bell ~6 inches above the floor to maintain a good stream profile. I assume the bell naturally isolate the heat from the floor, correct? Do you suppose I should try to isolate the entire heater from the back wall(s) and floor?
|
|
|
Post by peterberg on Oct 21, 2016 4:39:45 GMT -8
I understand the walls and floor are concrete. The floor will get warm(ish) very very slowly through conduction from the bell's walls, since the exhaust opening is well above the floor. No need to make a floor inside the bell, even mine is without any insulation or whatever down there, the walls are built straight on the tiles. The back wall could do with a 4" gap and that would be it. The concrete will warm up and provide more mass that way.
|
|
|
Post by peterberg on Oct 21, 2016 6:41:18 GMT -8
Oh, I have to say, the firebox floor of my heater is 1.5 ft above the floor so it won't heat up the floor that way.
|
|
|
Post by pinhead on Jan 10, 2017 16:46:00 GMT -8
I'm in the beginning stages of building this stove and am wondering about the ceiling of the bell. Especially due to the METAL IS DOOMED crowd (of which I'm a member).
I was going to support the roof of the bell with some fairly heavy angle-iron. However - after doing some measuring - it looks like the roof of the bell will be only about a foot away from the top of the heat riser. This leads me to believe that the angle iron will get hot enough to sag in the middle (I'm aware of the propensity of the expansion of the metal to shift the roof).
6-inch PBBB with P-Channel.
I understand that temperatures inside the heat riser are in the 2000 deg F range. My 7-inch PBBB has a fairly heavy angle-iron supporting the roof of the firebox and it hasn't shown any signs of wear in over two years of use. The normal "cap" of the stove is a steel barrel which is much thinner than the angle iron I had planned on using. The hottest I've seen the top of barrel is around 850 deg F. This leads me to believe that the angle iron will be up to the task.
So I guess, in a roundabout way, I'm asking those who know, "What is the best way to build the roof in such a bell?"
I have Rockwool, Ceramic-Fiber Blanket, angle iron, brick, clay, sand, and limestone at my disposal.
|
|
|
Post by Jura on Jan 11, 2017 0:41:11 GMT -8
At the top of the bell it is awfully hot, not good for steel objects, and down to the level of the riser is easy (for the gases). As I'm about to start a similar construction (the bell from the exemplary photo) but with a bench situated on a second floor I faced the same issue. (the system is supposed to direct flue gases either to the bell or the bench) and I was wondering if the sliding cast iron flap would be a choice good enough to be placed right beneath the bell ceiling. Will it survive long enough in there? I saw it applied at radek photo here & here
|
|
|
Post by satamax on Jan 11, 2017 0:56:32 GMT -8
Pinhead. I have thought about this. Puting a cast iron pot suspended over the heat riser, may be 20cm away. Could do the trick. On my workshop rocket, the ceiling of the fuel tank i used as a barrel, has sagged a bit under the concrete which is on top. I have 230 kilos there i think. Dropped down an inch, but more due to the fact that it can't expand lenghwise, son it's bulging. I haven't scraped the fly ash flakes there. But the metal having a heatsink right above, doesn't seem to have suffered that much.
|
|
|
Post by satamax on Jan 11, 2017 0:59:16 GMT -8
Heat damage on steels seem to occur above 400c to 600c iirc. It's what i remember from a documentary about sky scrapers.
|
|
|
Post by peterberg on Jan 11, 2017 2:23:47 GMT -8
If the use of angle iron above the riser is inescapable there are measures that could be taken to stay on the safe side. First: I would consider to use a heavy T-bar upside down, so part of that iron is out of the hottest zone. In that respect, an I-beam would be even better. Second: I'd keep it out of the area directly over the riser. I know of one guy who used this construction, his riser is in the middle and he divided the ceiling in three equal parts so the hottest spot is between two T-bars. Third: the iron could be wrapped in superwool so it isn't heated directly. I am ambivalent about this one, superwool being fluffy could be turn to rags over time without being seen. And oh yes, using something like superwool or ceramic paper between masonry and steel will give the steel room to expand and act as a slip joint.
|
|
|
Post by Vortex on Jan 11, 2017 6:01:00 GMT -8
I'm in the beginning stages of building this stove and am wondering about the ceiling of the bell. Especially due to the METAL IS DOOMED crowd (of which I'm a member). I was going to support the roof of the bell with some fairly heavy angle-iron. However - after doing some measuring - it looks like the roof of the bell will be only about a foot away from the top of the heat riser. This leads me to believe that the angle iron will get hot enough to sag in the middle (I'm aware of the propensity of the expansion of the metal to shift the roof). 6-inch PBBB with P-Channel. I understand that temperatures inside the heat riser are in the 2000 deg F range. My 7-inch PBBB has a fairly heavy angle-iron supporting the roof of the firebox and it hasn't shown any signs of wear in over two years of use. The normal "cap" of the stove is a steel barrel which is much thinner than the angle iron I had planned on using. The hottest I've seen the top of barrel is around 850 deg F. This leads me to believe that the angle iron will be up to the task. Yeah, if this was the case surely all those thin metal barrels would be burnt through the tops. You could use 'I' beams and firebrick, I've seen it done this way several times before (ends of the bricks inside the I's). You just have to make sure to leave expansion gaps for the steel to expand. The other option would be a large steel plate, half inch thick would do it. (That would give you some instant heat that you want.) If you cut out an expansion plate in the area above the riser (weld a thinner slightly larger piece on top of the bit you cut out and sit it back in the hole) it would avoid any warping of the plate and give you an easy cleanout/inspection point for the top of the riser.
|
|
|
Post by pinhead on Jan 11, 2017 7:49:57 GMT -8
|
|