|
Post by smartliketruck on Feb 25, 2018 17:17:31 GMT -8
A simple standardized, easy to construct burner to test the efficacy of refractory materials for rocket and related stoves would be great!
So my question to experienced rocketeers, what is the simplest, smallest and easiest to build standalone core that would prove a materials worth?
|
|
|
Post by esbjornaneer on Feb 28, 2018 3:19:05 GMT -8
Great SLT, I am interested in what the 'old timers' and others have to say.
|
|
|
Post by smartliketruck on Mar 14, 2018 12:10:20 GMT -8
I guess I'll start things off with my current plan. To test my current mixtures I'm going to build a 4 inch (100mm) plain Jane J tube, no p-channel, tripwires or kick tails. Dimensions will be when measure from next tubes centre line, 4 inch feed, 8 inch burn, 18 inch riser. In other words a 1:2:4.5 ratio.
Will the extra 0.5 height of the riser be enough to overcome the small system diameter?
Any other constructive input would also be appreciated.
|
|
|
Post by pigbuttons on Mar 14, 2018 18:09:51 GMT -8
I guess I'll start things off with my current plan. To test my current mixtures I'm going to build a 4 inch (100mm) plain Jane J tube, no p-channel, tripwires or kick tails. Dimensions will be when measure from next tubes centre line, 4 inch feed, 8 inch burn, 18 inch riser. In other words a 1:2:4.5 ratio. Will the extra 0.5 height of the riser be enough to overcome the small system diameter? Any other constructive input would also be appreciated. Good for you SLT. I'm not sure I understand your question on small system diameter. I've built a couple of fairly successful j-tubes that are square in cross section and are 4" and they run just fine. I don't quite understand the ratios being used. When I first started researching rocket stoves the only dimension that was affirmed to be necessary was that the length of the burn tunnel was 4 times the diameter of the tunnel measured from the centerlines of the feed tube and riser. Mine are actually only about 3 times and they run fine but sometimes the flames come up the riser about three or four inches. Anyway, please keep us posted. I for one am very interested in your results.
|
|
|
Post by smartliketruck on Mar 14, 2018 18:31:18 GMT -8
Hey pigbuttons, I was using this thread donkey32.proboards.com/thread/1170/tube-dimensions as a starting point. It's my understanding that less than 6 inch J tubes can be finicky so thats why I was planning to make the riser a little taller. If it would still get to rockety temperatures with a shorter burn tube or riser I'm all ears. If it could reliably come to rockety temperatures with darn near any material at a smaller system diameter all the better.
|
|
|
Post by smartliketruck on Mar 15, 2018 10:32:14 GMT -8
|
|
|
Post by smartliketruck on Mar 16, 2018 11:38:33 GMT -8
The 1:2:5 ratio works well if making a square scrapwood form so that you can reuse the pieces of the base for the riser. 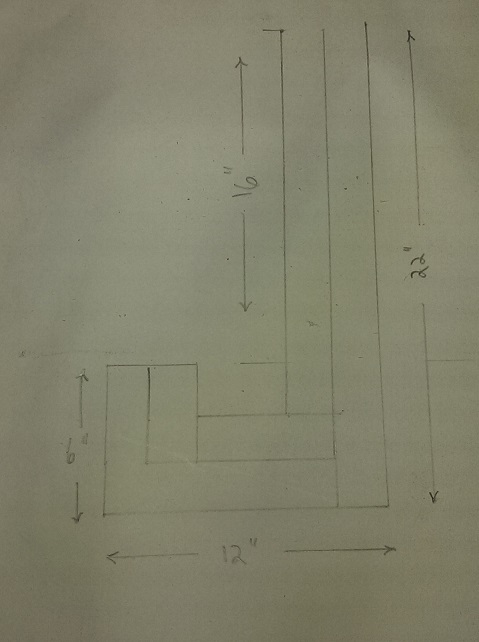 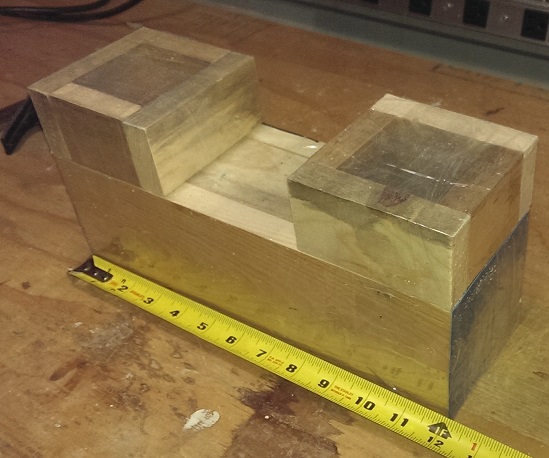 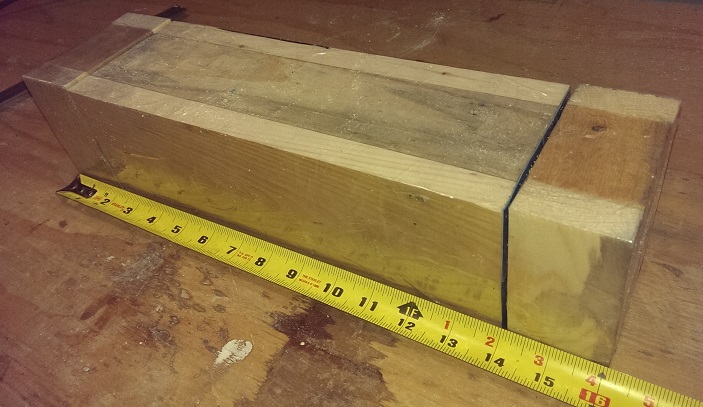 If you want to raid the recycle bin for materials, I found a stewed tomato can is damn near 4 inches as well as 2 liter paper milk cartons
|
|
|
Post by smartliketruck on Mar 16, 2018 18:30:37 GMT -8
First lift of base has been poured, now I'll let it setup, cut some indexing notches, coat the mating surface with vegetable oil and pour the second lift. 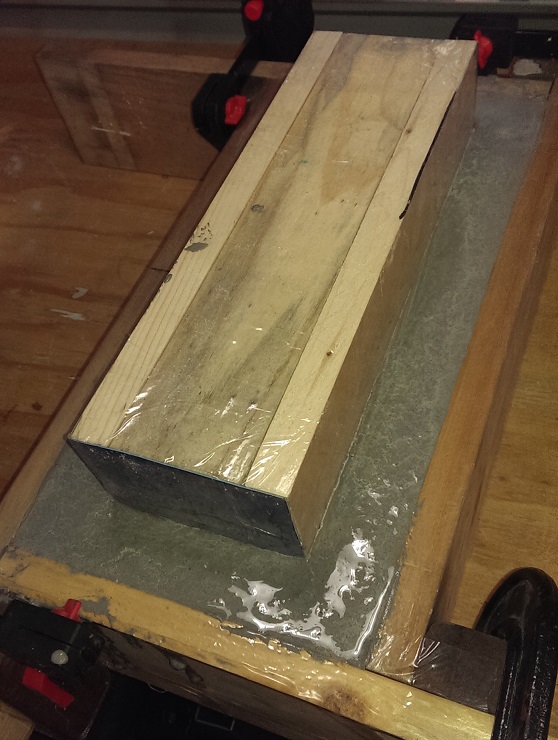 New territory for me here, wish me luck.
|
|
|
Post by Orange on Mar 17, 2018 5:20:04 GMT -8
|
|
|
Post by smartliketruck on Mar 17, 2018 10:59:06 GMT -8
I've sort of veered away from the original intention of the thread and have turned it into a build thread. I'll edit some of my previous posts to simplify and post a proper build thread when this core is done. In the mean time the base of this core is in the oven for it's warm wet cure.
|
|
|
Post by smartliketruck on Mar 17, 2018 22:46:09 GMT -8
Fail! Whenever I've used wood for a form/mold I guess I've always stripped it early. Even with a heavy douse of packing tape water will get to where it wants. The wood swelled and broke everything from the inside out. Back to the drawing board and more fodder for the grog pile.
I wonder if I can get away with using free EPS foam packaging rather than buying sheets of XPS for the internal form?
It might seem I'm being penny wise and pound foolish with this but it would be nice if anyone on any budget could make a test core that can be measured in the same ballpark as others with as few red herrings as possible.
|
|
|
Post by etownandrew on Mar 18, 2018 4:59:29 GMT -8
Fail! Whenever I've used wood for a form/mold I guess I've always stripped it early. Even with a heavy douse of packing tape water will get to where it wants. The wood swelled and broke everything from the inside out. Back to the drawing board and more fodder for the grog pile. I wonder if I can get away with using free EPS foam packaging rather than buying sheets of XPS for the internal form? It might seem I'm being penny wise and pound foolish with this but it would be nice if anyone on any budget could make a test core that can be measured in the same ballpark as others with as few red herrings as possible. This is a good warning. I had bought a sheet of plywood to construct a form. I will need to think about this more. One thought I had been considering was making the wood form an exterior one and lay up the stove core clay, etc on the inside. That way the wood swelling and clay shrinking would not be in conflict.
|
|
|
Post by Vortex on Mar 18, 2018 5:30:10 GMT -8
I've never had any problems with wood forms but I always give them a good soaking with linseed oil before and after using them so maybe that gives them some waterproofing.
|
|
|
Post by pigbuttons on Mar 18, 2018 5:48:12 GMT -8
I use styrofoam sheets that come in a 1 ft by 4 ft pack of 6, 1 inch sheets, and just glue them together to form larger blocks. It cuts easily, will tolerate the pressure of some pretty aggressive packing tamping, is water proof so it does not steal needed moisture from the mix, will not shrink or expand from water or the minor heat of curing, can be removed by cutting it out with a knife after curing is complete, is available at most hobby or craft stores. For the exterior it would need to be supported with something solid.
|
|
|
Post by smartliketruck on Mar 18, 2018 9:39:02 GMT -8
etownandrew Vortex : My internal form had nothing in the way of an expansion/contraction joint, so taking that into account if I need to go that route again should help. I have my doubts that linseed treated wood would have help substantially in the conditions I was subjecting it to, 185°F/85°C and a extremely high water mixture wrapped in pallet stretch wrap. I definitely need to treat my cottle boards with something though rather than re-applying packing tape every time, linseed oil is top of the list. pigbuttons : Are you using a specialty adhesive for your foam sheets? Would cheap & widely available ABS plumbers cement work?
|
|