|
Post by Donkey on Feb 1, 2009 9:23:29 GMT -8
I've been going on about tapered heat risers for some time now. Over the last few months, I've actually done something about it. Or at least a little something about it. First, I went and got a log.. I placed the log on a lathe and lathed out the male positive for the inside tapered shape. The narrow end is six inches diameter and the wide end eight inches. The shape between the two was sort of a touchy-feely thing.. I didn't use any formula (though I imagine there would be an optimum one), just did what "felt right". I then let the lathed log sit around in a dry place and finish curing. After the log was ready, I patched checks and cracks with wood putty, sanded it all smooth and painted it with some old leftover exterior house-paint that I've got laying around. At the dump I found a big stainless steel water filter canister that would be perfect for an exterior jacket. So I cut off the ends and taped closed a hole where some pipe had previously stuck out. Then I made a base piece for my log, one that would slide inside the stainless jacket to seal it and butt against and form a handle to pull it out later.  My first attempt at molding a heat riser with this arrangement was a total disaster.  I thought that the house-paint would be enough to keep castable refractory from sticking to it.. Oops!! I actually had to beat the thing apart with a sledge to get the mold back out again. So, I tried again.. This time I used a pearlite/clay mixture. In case things go south, I can knock it up, add water and re-use. I've been curious about using this stuff without a covering anyway, so what the heck.. This time, I wrapped the male portion of the mold in plastic before pouring in the mix..  It appears to have worked. It ain't the smoothest inside, but it looks serviceable. At this time, I'm still waiting for it to dry completely. I've taken it outside to sit in the (unseasonably warm) sun.. Hopefully in a couple/few days it will be completely dry and ready to test run.
|
|
|
Post by canyon on Feb 1, 2009 13:38:49 GMT -8
Awesome Donkey, thanks for sharing. I think this kind of thing is where it is at. Is a heart shaped vortexer next? 
|
|
|
Post by Donkey on Feb 1, 2009 17:58:50 GMT -8
I'm thinking that the sudden expansion from a six inch (28.26 sq. in.), square, brick made opening to an 8 inch round shape may create enough turbulence on it's own. Look up "bluff body" in wikipedia. Though, yes... I WILL be trying out said turbulator at a later date.
|
|
|
Post by johnjmw on Feb 3, 2009 6:09:18 GMT -8
Alright, this is one of your threads I've eagerly been waiting for someone to try. I keep thinking there will be a torch like effect at the exit of the heat riser. The casting of the insulated heat riser is also an idea worth the work, esp if it is strong enough to not get crumbly after a few firings. Wasn't that a problem with the sawdust/clay riser you made preveously John
|
|
|
Post by Donkey on Feb 4, 2009 6:59:02 GMT -8
Yeah, the sawdust/clay did get crumbly. I don't think they are equivalent though, the sawdust burned out, which pearlite will not do. I've been thinking that in a more "final" version, I would coat the inside with waterglass or perhaps a thin "plaster" of waterglass/clay. Or perhaps mix a little waterglass in with the pearlite/clay before it's put into the mold.
|
|
|
Post by johnjmw on Feb 5, 2009 4:43:42 GMT -8
Sorry for my lack of knowledge, but what would adding the waterglass gain the system? I was under the impression that it is just more insulation. Ok, more insulation possibly a hotter burn in the riser? John
|
|
|
Post by Donkey on Feb 5, 2009 9:03:13 GMT -8
Waterglass, also known as sodium silicate, is a commonly used binder and coating in kilns and whatnot. I don't think it would add any insulating qualities, it's just a thin layer. I think it would protect the surface of the heat riser. Kinda bind it together and keep it from crumbling.. ??
|
|
|
Post by johnjmw on Feb 7, 2009 6:22:32 GMT -8
Ok that makes sense. Also a smoother surface for better air flow. About how much did the cast riser weigh made from the pearlite and clay? Something one person can hustle arround with out straining himself? Or a two man job?
|
|
|
Post by Donkey on Feb 7, 2009 10:08:32 GMT -8
It's really light.. I just had to move it back inside so as not to get rained on.. It's STILL wet from pouring it, but quite light weight. It seems that the metal jacket might be just about as heavy as the pearlite/clay bits.
I'm beginning to change my mind somewhat about smooth surfaces inside the stove. It appears that what's needed is as much turbulence as possible. Turbulence for fuel/air mix in the burn process and turbulence for better distribution of heat later on.. Seems to me that this is a critical area for investigation.. How much is too much, too little, where do you want a turbulent environment and where a laminar one??
|
|
|
Post by canyon on Feb 8, 2009 0:11:11 GMT -8
Balance of the system in particular is the key. There is a difference between turbulence and drag. If the system has a long heat exchanger gas path you might want a smoother surface for less drag. In the combustion/heat riser area the more turbulence/gas mixing the better. The shorter the heat exchanger path the more turbulence helps. I think the proof is in the exit temp (mid flow). 
|
|
johnf
New Member
Posts: 18
|
Post by johnf on May 1, 2009 17:01:33 GMT -8
I just caught this: It's something I'm exerimenting on with small DIY things. If the vertical airflow is given a mixing motion, it inreases mixture without sacrificing fast flow. Magh(cloud) twister e-twisterstove.blogspot.com/(Is this concept like the tapered heat riser mentioned here?) penny wood stove 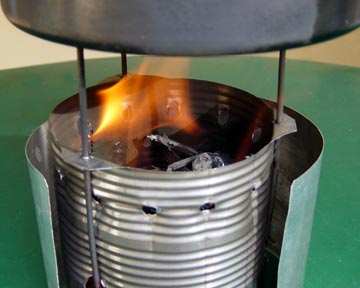 It seems the big household "rocket" burners for heating cob masses use a very tall burn tube (up to 50"/~120cm) to maximize time. Balance of the system in particular is the key. There is a difference between turbulence and drag. If the system has a long heat exchanger gas path you might want a smoother surface for less drag. In the combustion/heat riser area the more turbulence/gas mixing the better. The shorter the heat exchanger path the more turbulence helps. I think the proof is in the exit temp (mid flow). 
|
|
|
Post by Donkey on May 3, 2009 9:09:37 GMT -8
Yep. The expansion chamber below (widened riser at bottom) should produce a good deal of turbulence, improving mixing, without introducing gizmos into the flow.. Tapered towards the top to increase velocity and hopefully concentrate heat.
I've test fired it once. Though the works were still somewhat damp, it ran well. It's raining now and I've got a paying rocket stove sauna gig, so my testing on this stove is temporarily on hold.. I've got to leave next week to go teach for a couple weeks.. I likely wont get back to the tapered stove till sometime in June at the earliest.
|
|
|
Post by canyon on May 3, 2009 22:42:57 GMT -8
Hey Johnf, thanks for posting that link. Very interesting. Some of the fire swirling pictures are amazingly beautiful. I hope to see one of these twister stoves sometime. Donkey some of us are waiting with baited breath on your tapered mold project results.  Your sauna project looks like fun! Thanks for keeping us updated.
|
|
|
Post by Donkey on Jul 1, 2009 6:28:03 GMT -8
Well... I've used the tapered heat riser stove a couple-few times now.. It works great and all, but I'm not really seeing a BIG difference. Not yet.. So far --- Inconclusive.
|
|
|
Post by Donkey on Aug 8, 2009 9:51:05 GMT -8
Ok, I've tried something a little different. A gradual (stepped) widening of the burn tunnel, till it reaches the bottom of the tapered riser.
Here I'm seeing quite a difference from before. Still, I'm not seeing (much) more than I've gotten from a straight riser in the past. Seems as though the difference between ho-hum performance and outta sight is a little tuning.. I kinda knew that already, but the more I play, the more evident it is.
I'll post the internal measurements (maybe some pics too) possibly later this afternoon or tomorrow.
|
|