|
Post by peterberg on May 16, 2017 12:20:20 GMT -8
Question no. 10:I was just trying to calculate the dimensions of the floor channel for 180mm system... All info is well presented at batchrocket.eu, except the height of vertical part of floor channel... I don't recall it being explained anywhere... By feel i would say that it is in some proportion to the port height? Yes, it is, it could be deducted out of the dimensions in the drawing. But to make things simple: the total height of the vertical part is 1xbase, a little bit lower or halfway up the port. Mine is halfway, I just checked it. I did a detailed sketch of the firebox door frame and the door... they will be made of stainless steel, T (30x30x4 mm) and U (80x40x4mm) profiles used for the main part. The majority of the design for the doors is "stealed" from here. Knowledge that's open source can't be stolen, just used! The blue line shows where the 8mm sealing cheramic will be present. You need tolerance between the door and its frame because the door will expand quite a bit. I made the door all around 4 mm smaller than the frame and used a 6 mm stove rope right in the corner of the T-profile. This works very well, the steel of the door still touch the frame and the door is very tight. In the next image there are two metal rectangles market with red. They are movable from the inside. Once the stove will be fine tuned, they will be fixed in place. I prefer to have slightly too large inlet at first, just in case... Or do you think this is an overkill? The primary air intake is tilting to open... The tilting valve I made has two triangle pieces left and right, the opening can be tuned with two small bolts. Also, there need to be a weight on the inside of the valve to keep it closed. Balanced with the valve itself so when it's open it will stay that way as well. When started, the opening is 25 x 150 mm. When at full burn in a warm heater, the opening of my inlet is no more than 15 x 150 mm. I would say you need something that can be open in two adjustable positions. I am concerned because the floor channel tube is not in the middle but on the right... I think that it will be better to put the primary air opening to the right so that the floor channel gets the air with least restriction... Would you agree or it doesn't matter significantly... I think the air inlet can be in the middle without repercussions provided there's also a threshold the width of the door frame above the floor channel opening. In my heater this is almost as high as the sloped sides of the firebox. An added bonus is that the ash won't block the floor channel as easily. It could be welded in the door frame for convenience. Mine is mounted on the floor channel but in practise I did't take it out in two years. By the way, the picture don't show this, it's one of the numerous configurations during the first winter.
|
|
dvawolk
Full Member
 
DSR2 125mm open system (actual project)
Posts: 272
|
Post by dvawolk on May 16, 2017 20:58:49 GMT -8
Good morning! You need tolerance between the door and its frame because the door will expand quite a bit. I made the door all around 4 mm smaller than the frame and used a 6 mm stove rope right in the corner of the T-profile. This works very well, the steel of the door still touch the frame and the door is very tight. Hm, i was thinking about the tolerance when opening the door (diagonal length) but i didn't take into the account the thermal expansion... But i checked it on online thermal expansion calculator if the difference in temperature comes to 400 (and the frame stays still cool), the door would be 1,5mm wider and 2,2mm higher... But I am quite sure that the door wont heat that much... I will stretch the door frame few millimeters to be safe... The tilting valve I made has two triangle pieces left and right, the opening can be tuned with two small bolts. Also, there need to be a weight on the inside of the valve to keep it closed. Balanced with the valve itself so when it's open it will stay that way as well. When started, the opening is 25 x 150 mm. When at full burn in a warm heater, the opening of my inlet is no more than 15 x 150 mm. I would say you need something that can be open in two adjustable positions. Great, i was thinking to implement the counter-weight, too. Using the triangles to hold the inlet door you can only have or totally open or totally closed door. I will tinker about two adjustable options... Maybe with a spring with two gaps or two magnets that can be fastened to a desired space... I like magnets option:-) My full primary inlet for 180mm should be 20% of CSA, which comes to just over 50 cm 2. Below is a quick brainstorm sketch for primary inlet with door magnets (red), closed, half open and full open. I can get magnets with hole, so adjustment and fastening is not a problem... I think this might work... The blue square is the weight.  I think the air inlet can be in the middle without repercussions provided there's also a threshold the width of the door frame above the floor channel opening. In my heater this is almost as high as the sloped sides of the firebox. An added bonus is that the ash won't block the floor channel as easily. It could be welded in the door frame for convenience. Mine is mounted on the floor channel but in practise I did't take it out in two years. Ok. I remember that trapezoidal threshold in your Sketchup drawing of a casted red bell heater.. Because it was attached to the floor channel it seemed to me that cleaning the ashes out of the firebox was an unconvenient task.... I will rather implement it on the door frame in the folowing versions of Sketchup... Question no. 11Looking at the next picture... How significant is the red (distance from the back wall of firebox to the port) and the blue dimension (distance from the port to the begining of a slope)? Question no. 12Regarding the below picture... I changed the dimesions of the slopes so that the one near the port is higher and the one on the other side is lower... That way longer fuel is easily loaded into the firebox... The vertical part of the floor channel is less in the way... It seemed to me a good idea - but is it? :-)  Best regards, Klemen
|
|
grga
Junior Member

Posts: 76
|
Post by grga on May 17, 2017 23:49:15 GMT -8
Hi, this seems to be another great project of yours.
I would suggest the following:
- Moving floor channel in the middle of the burn chamber as in regular straight design. It would be a bit more work with welding. But bonus is that you can easily take it out and clean also floor in the riser…
- Oven I think it would be wiser to position so that its bottom is also top of the main burn chamber. Maybe you can put for the top of the burn chamber 6 cm schamote to lower the temperature loss of the chamber and still have enough in the oven. This way the oven would be hot enough (for sure at the floor and probably also at the top) more likely.
- Your entry to the chimney is cca 160 cm from the floor. I do have similar situation. I was thinking to make another opening to the chimney at the floor level to the existing schiedel pipes in the wall. Then there will be no need for additional chimney in the bell. But you can make bypass only at current height of the chimney entry. On the other side of the wall you probably have chimney doors as I do so you can use them to monitor operation…
And my question/thought: I like side version of the batchbox as it need more than 20 cm less depth of the fireplace. But is its operation still similarly effective – the fire need to make two 90 degree turns to run in the riser – is this good or not? I will soon start with my design very probably also 18 cm straight cast version however I may change my plan to the side version.
If you not so much in a hurry we could also make two casts in the same mold as we are only 30 km apart? My firs experimental 12 cm cast seems to be fine after more than 20 runs it only have a few minor cracks from the first two runs. It might be too soon to tell. I have used CAC cement however you can also use factory mix.
If not too much work is it also possible to post Skechup 8 version.
|
|
|
Post by peterberg on May 18, 2017 0:41:40 GMT -8
But i checked it on online thermal expansion calculator if the difference in temperature comes to 400 (and the frame stays still cool), the door would be 1,5mm wider and 2,2mm higher... But I am quite sure that the door wont heat that much... I will stretch the door frame few millimeters to be safe... I wouldn't be surprised if the top part of the door could reach that 400º C. I will tinker about two adjustable options... Maybe with a spring with two gaps or two magnets that can be fastened to a desired space... I like magnets option:-) My full primary inlet for 180mm should be 20% of CSA, which comes to just over 50 cm 2. Personally, I would go for the magnet option. Heat might change the properties of springs. I remember that trapezoidal threshold in your Sketchup drawing of a casted red bell heater.. Because it was attached to the floor channel it seemed to me that cleaning the ashes out of the firebox was an unconvenient task.... I will rather implement it on the door frame in the folowing versions of Sketchup... I use an old fashioned coal scoop which I operate sideways. Not all the ashes could be cleaned out this way but it's a good thing to have some ash layer at the floor channel anyway. One curious observation: when there are nails in the fuel the resulting coals are less... Question no. 11Looking at the next picture... How significant is the red (distance from the back wall of firebox to the port) and the blue dimension (distance from the port to the begining of a slope)? There is a marked difference when the port is directly flush with the back wall, in a negative way. For convenience I would say the distance to the back wall should be 0.5 to 0.75 times Base figure. That last figure is the same distance to the back wall corner in both directions as in the straight version. Same goes for the distance to the sloped side. Question no. 12I changed the dimensions of the slopes so that the one near the port is higher and the one on the other side is lower... That way longer fuel is easily loaded into the firebox... The vertical part of the floor channel is less in the way... It seemed to me a good idea - but is it? :-) I my view, it doesn't make a difference provided the overall dimensions are respected. See it this way: the double vortex doesn't know about what is happening in the firebox as long there're enough combustibles produced and the streams to the port keeps going.
|
|
|
Post by peterberg on May 18, 2017 0:57:06 GMT -8
Moving floor channel in the middle of the burn chamber as in regular straight design. It would be a bit more work with welding. But bonus is that you can easily take it out and clean also floor in the riser… Good point, in the construction shown the triangular bricks at the port side should be removable in order to allow replacement of the floor channel. And my question/thought: I like side version of the batchbox as it need more than 20 cm less depth of the fireplace. But is its operation still similarly effective – the fire need to make two 90 degree turns to run in the riser – is this good or not? Yasin Gach used a Testo to a prototype sidewinder with floor channel. It did extremely wel, and a bigger demonstration version worked even better. In general: the bigger the system, the ratio between volume and wall area becomes much more favourable. More turns don't do the double vortex any harm, like Matt's experiments showed. The single downside is it will take longer for the afterburner to catch on when started when it's farther away from the firebox. This is less important in a system that's ran hours on end, of course.
|
|
dvawolk
Full Member
 
DSR2 125mm open system (actual project)
Posts: 272
|
Post by dvawolk on May 18, 2017 4:01:32 GMT -8
Moving floor channel in the middle of the burn chamber as in regular straight design. It would be a bit more work with welding. But bonus is that you can easily take it out and clean also floor in the riser… Hi, grga. Where are you from? I did a casting of 4" batchbox but it seemed to be too small of a system. I used castable refractory from TOGO, Slovenia... It is quite pricey... The floor channel will be removable.. Those triangular bricks on the right will be removable, i am thinking of fixing them together with refractory mortar to be more stable - if they are bound together, i am sure that they will not move easily... Or maybe instead of using refractory mortar, i might just drill two holes through them and fix them with a metal rod that will be bent in the end... Oven I think it would be wiser to position so that its bottom is also top of the main burn chamber. Maybe you can put for the top of the burn chamber 6 cm schamote to lower the temperature loss of the chamber and still have enough in the oven. This way the oven would be hot enough (for sure at the floor and probably also at the top) more likely. Hm , that would be interesting... If oven is in the middle of the bell, the temperature above will be slightly more than below. But i think that in these 25cm differences in height that would not be much of a visible difference... But if i put the oven directly over the firebox... Hm, grga, have you been trying anything about that? You mean that 6cm chamotte in thickness is okay for a single firing to reach a more or less desired temerature? It would be nice if radek comes by and says a word or two regarding the ovens - i know he has done some of them... Below again is the photo of the oven that i will use... It has a frame and at the back it has to be supported... Putting it directly on top of the 6cm thick chamotte over the fireboxwould make things much easier...  Your entry to the chimney is cca 160 cm from the floor. I do have similar situation. I was thinking to make another opening to the chimney at the floor level to the existing schiedel pipes in the wall. Then there will be no need for additional chimney in the bell. But you can make bypass only at current height of the chimney entry. On the other side of the wall you probably have chimney doors as I do so you can use them to monitor operation... My entry to the chimney is 205cm high... The cleaning door are on the other side of the wall, about 80-100cm high... 20cm high from the floor is condensation pipe coming out from the chimney (on the other side of the wall)... I prefer to leave existing chimney flues as they are (at least for this project)... If you not so much in a hurry we could also make two casts in the same mold as we are only 30 km apart? My firs experimental 12 cm cast seems to be fine after more than 20 runs it only have a few minor cracks from the first two runs. It might be too soon to tell. I have used CAC cement however you can also use factory mix I think i will stay away from castable refractory for now.. I intend to buy a table saw for wet cutting of bricks in the next days, so it is much easier to play with different sizes/shapes of bricks... But it is a pricey thing. But anyway, i don't want this heater to be my last build. Having a good saw at hand is a nice excuse to make another project:-) If not too much work is it also possible to post Skechup 8 version. Below is the V8 sketchup file... But tomorrow i will update it so that i implement all the accepted details... V8 Sketchup File
|
|
dvawolk
Full Member
 
DSR2 125mm open system (actual project)
Posts: 272
|
Post by dvawolk on May 18, 2017 4:14:06 GMT -8
I wouldn't be surprised if the top part of the door could reach that 400º C. Adding another millimeter of gap to be sure! This will be interesting to observe in action! Personally, I would go for the magnet option. Heat might change the properties of springs. I agree! I prefer magnets instead of thin springs... There is a marked difference when the port is directly flush with the back wall, in a negative way. For convenience I would say the distance to the back wall should be 0.5 to 0.75 times Base figure. That last figure is the same distance to the back wall corner in both directions as in the straight version. Same goes for the distance to the sloped side. I my view, it doesn't make a difference provided the overall dimensions are respected. See it this way: the double vortex doesn't know about what is happening in the firebox as long there're enough combustibles produced and the streams to the port keeps going. Okay. I will fix this.. Also i think i will lengthen the firebox for about 5cm so that it can easily handle 0,33 meters long fuel pieces... If i recall correctly, the fuel can be directly behind the floor channel when there is a straight (not sidewinder) core... But it doesn't feel good if the fuel touches the side of the channel as might be the case here if the firebox is too short... In practice, occasional longer fuel can be added behind the channel on the left of the firebox. But leaning on it is probably not a good thing...? Best regards, Klemen
|
|
grga
Junior Member

Posts: 76
|
Post by grga on May 18, 2017 4:39:40 GMT -8
Hi Klemen, I am from Ljubljana and you have showed me your rocket about half a year ago if you remember… Regarding the oven, I tried to place it quite high in the bell, it was made from 3cm bricks and I could not reach very high temperatures maybe around cca. 200 (not close enough to make pizza). I know that the batch box gets very hot from the outside for sure enough to bake pizza and the rest of the oven should also heat from the bell so it should be evenly heated. I saw the idea of placing the oven first here: wildflowerdays.com/2014/11/08/masonry-heater-again-for-men-only-jk-craigs-idea-to-write-that/and one is also here at bilbius: donkey32.proboards.com/thread/2272/hydronic-heating-bbr-project. I am guessing that this should work and is simple to place. However it is not so nice to have the oven low for your back and visually – however if you do make one it should work fine.
|
|
dvawolk
Full Member
 
DSR2 125mm open system (actual project)
Posts: 272
|
Post by dvawolk on May 18, 2017 12:12:04 GMT -8
Hi Klemen, I am from Ljubljana and you have showed me your rocket about half a year ago if you remember… Regarding the oven, I tried to place it quite high in the bell, it was made from 3cm bricks and I could not reach very high temperatures maybe around cca. 200 (not close enough to make pizza). I know that the batch box gets very hot from the outside for sure enough to bake pizza and the rest of the oven should also heat from the bell so it should be evenly heated. Yes, i do remember now :-). So you did 120mm batchbox? And you implemented an oven in its bell? I would say that it is much different to have a chamotte white oven or metal oven in the bell. I would go only form chamotte black oven... I doubt that white oven made of chamotte would heat enough... Thinking further, i too imagine that the ceiling 6cm thick above firebox would heat enough. If i put a metal white oven over it, i would seal the bottom gaps so that just a few centimeters of dead air would be present between hot chamotte below and iron floor of oven above... It should be heated enough from below, but slightly less above... I think that this oven (if put on firebox ceiling) would get hotter at the bottom than a the top even in the middle of a full burn... Lower positioned oven does demand some bending over for grown-ups, but there are pros, too. The kids like to see what is going on and they are encouraged to make bread/ pizza on their own... And the owner of this heater might positively oriented towards kids-friendly oven :-) * Myself, i like baking bread/pizza directly on the chamotte floor... Maybe in a future build it may be a good option for the oven to be chamotte firebox floor below and just a metal part above it... I like this idea, i might try it some day. I think that it would work best if the height inside the oven would be lower as usual - so that the whole volume of this oven would be heated mainly from the chamotte slab below.. But this is another project.. Regards, Klemen
|
|
|
Post by bulbius on May 18, 2017 13:28:46 GMT -8
Personally, I would go for the magnet option. Heat might change the properties of springs. I agree! I prefer magnets instead of thin springs... beware that also magnets can loose their properties after exposition to high temperatures, neodymium magnets can loose permanently some of magnetization after 80° C, ferrite magnets after 250° C. One day I placed many magnets around the barrel of my rocket stove and after half an hour they have begun to fall!!
|
|
dvawolk
Full Member
 
DSR2 125mm open system (actual project)
Posts: 272
|
Post by dvawolk on May 18, 2017 19:54:57 GMT -8
beware that also magnets can loose their properties after exposition to high temperatures, neodymium magnets can loose permanently some of magnetization after 80° C, ferrite magnets after 250° C. One day I placed many magnets around the barrel of my rocket stove and after half an hour they have begun to fall!! OH, I have to try that. They would surely be heated above 80 °C... I thought that magnets loose properties when arriving towards the red-hot...
|
|
dvawolk
Full Member
 
DSR2 125mm open system (actual project)
Posts: 272
|
Post by dvawolk on May 20, 2017 6:04:45 GMT -8
I searched for some info regarding neodymium magnets - i guess this is not an option... I will think about other solutions of having a simple two-step air inlet door... HERE is the sketchup version of an updated core with door... The door have now an air diverter (screenwash?) fixed to it... But user will have to be careful not to touch it accidentally when refueling the firebox... Also, below are some images.    One question, peterberg , as you mentioned that the vertical part of the floor channel is 1x base number. In 180mm system that would be 13cm... But where exactly this measure is to be applied (see photo below) A, B or C?  Implemented details for the whole 3D drawing are coming soon...
|
|
|
Post by peterberg on May 20, 2017 10:08:35 GMT -8
The door have now an air diverter (screenwash?) fixed to it... But user will have to be careful not to touch it accidentally when refueling the firebox... First, I wouldn't do it like that, ash will fall out everytime the door is opened. What's more, one single piece of fuel that's 5 mm too long and the door won't close until you have taken that darn piece out... Since you want to make the threshold removable, mount it with two lips or locating pins or whatever on the door frame, not on the door itself. Another thought: what I have at home is an angled piece of steel mounted on the threshold in such a way that the opening between the door profile directly above the inlet and that angled piece is no wider than 12 mm, over the entire width of the door. My heater is a 150 mm system so you need to convert it to the size you are planned to build. That restricted opening is doing the trick in my case. One question, peterberg , as you mentioned that the vertical part of the floor channel is 1x base number. In 180mm system that would be 13cm... But where exactly this measure is to be applied (see photo below) A, B or C? Can't see the picture, but this vertical piece is measured from the top of the horizontal part, i.e. the firebox floor. The same as the height of the firebox and the height of the riser, trying to be consistent.
|
|
dvawolk
Full Member
 
DSR2 125mm open system (actual project)
Posts: 272
|
Post by dvawolk on May 20, 2017 12:03:21 GMT -8
First, I wouldn't do it like that, ash will fall out everytime the door is opened. What's more, one single piece of fuel that's 5 mm too long and the door won't close until you have taken that darn piece out... Since you want to make the threshold removable, mount it with two lips or locating pins or whatever on the door frame, not on the door itself. Another thought: what I have at home is an angled piece of steel mounted on the threshold in such a way that the opening between the door profile directly above the inlet and that angled piece is no wider than 12 mm, over the entire width of the door. My heater is a 150 mm system so you need to convert it to the size you are planned to build. That restricted opening is doing the trick in my case. I really like that the threshold is removable... Cleaning my batchbox without threshold couldn't be easier... One can clean it with one stroke towards the door... Why should the threshold be present? Is it only for the safety because of coals falling out or does it effect the ratio of primary/secondary air input? This firebox is now 39cm long from the begining of chamotte to the end of the right slope. And the length of the fuel will be 33cm... Also, the total length of a firebox ( to the back wall) is almost 60cm, which is enough even for ocasional much longer piece of wood ( i imagine that it wouldn't be a problem even to the length of 50cm). peterberg , are you talking about below threshold from your site? And as i have seen the casted red bell doesn't have this metal insert (on the photo when burning)... 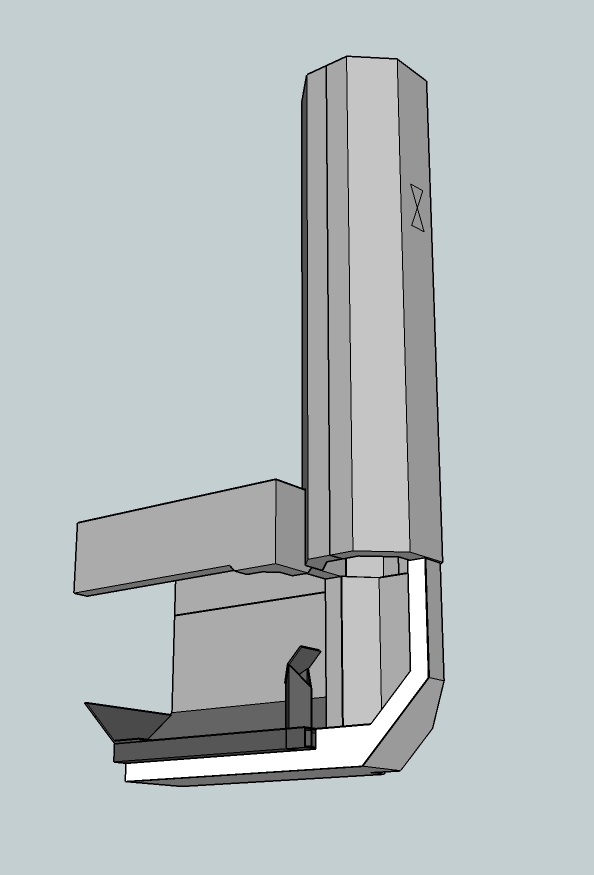 Glass with my batchbox is really clean. I clean it 1-2 per season but not because it is black - it just becomes slightly tinted from the gases... Anyway i can easily put it on the door frame to stay removable. Something like that:  One question, peterberg , as you mentioned that the vertical part of the floor channel is 1x base number. In 180mm system that would be 13cm... But where exactly this measure is to be applied (see photo below) A, B or C? Can't see the picture, but this vertical piece is measured from the top of the horizontal part, i.e. the firebox floor. The same as the height of the firebox and the height of the riser, trying to be consistent. I updated the previous post, image is now seen. I did measure it from the firebox floor but i am not sure to where it is measured above :-) I guess it is C version?! Regards, Klemen
|
|
|
Post by peterberg on May 20, 2017 13:07:01 GMT -8
Why should the threshold be present? Is it only for the safety because of coals falling out or does it effect the ratio of primary/secondary air input? This firebox is now 39cm long from the begining of chamotte to the end of the right slope. And the length of the fuel will be 33cm... Also, the total length of a firebox ( to the back wall) is almost 60cm, which is enough even for ocasional much longer piece of wood ( i imagine that it wouldn't be a problem even to the length of 50cm). To avoid telling this story over and over again: please read this thread on permies.com. I am quite sure I wrote an explanation on this forum too, but can't find it. It has all to do with laws of physics: in particular the one that dictates that hot air is lighter as compared to colder air. Since this law won't be lifted in the foreseeable future, it will work as described. peterberg , are you talking about below threshold from your site? And as i have seen the casted red bell doesn't have this metal insert (on the photo when burning)... I know that, that's a picture been taken during the development stages without this particular feature. I'll try to take a picture tomorrow morning of the current threshold plus the angular steel profile. Anyway i can easily put it on the door frame to stay removable. The threshold doesn't need to be traingular or a trapezium. Of course you are entitled to build what you like, but I am pretty sure the results won't be the same as the thoroughly tested reference design, my red bell heater. I updated the previous post, image is now seen. I did measure it from the firebox floor but i am not sure to where it is measured above :-) I guess it is C version? Yes it is C, somewhere I wrote it is the total height, so it couldn't be something else... I've found the other explanation: please read that too.
|
|