|
Post by peterberg on Jan 19, 2017 5:55:41 GMT -8
Perhaps this isn't a good title, but it can be changed anytime (or so it seems). Two years ago, our member Jono (Jonathan Hughes) tried an idea for a cooking device, something like the Aprovecho Institutional Stove. Eventually, he came up with a hybrid between a batchrocket and Winiarsky's rocket cooking stove. And I have to emphasize, with a new twist to it. The twist is the addition of a venturi or "port" as we like to call it. Jono's wanderings ended with a 55 gal. barrel, a 100 liter pot with a very simple, self feeding casted combustion core underneath it. At the time, I said this could be worth to investigate further, and last fall I finally did. I started off gathering all the pieces of vermiculite board I had lying around, left-overs from another build. This material was assembled more or less in an L-tube of 10 cm (4") square. At the back I mounted two pieces of stainless steel, left and right in a slit cut in the vermiculite board. So there was an opening left of about 60% of the cross section area, not like the straight batch box vertically but under 45 degrees instead. The idea was to build a compact core, the riser on top of the firebox. 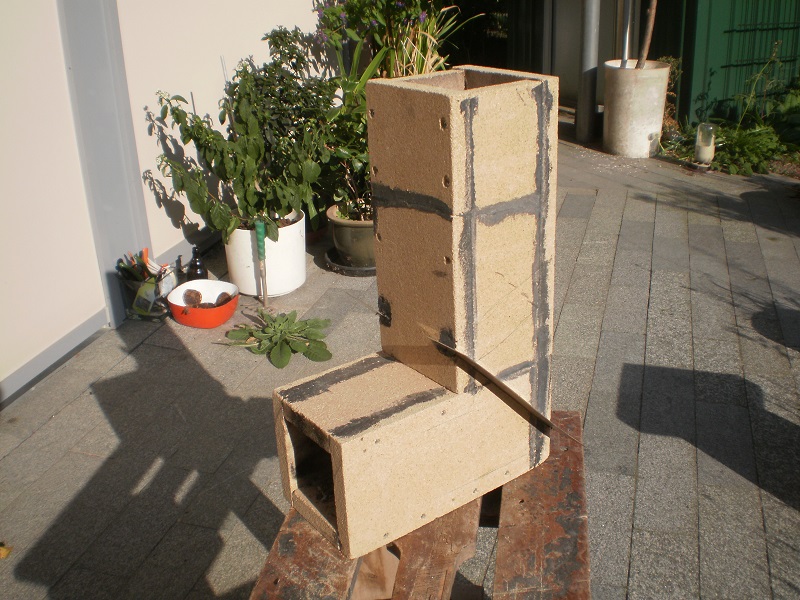 Seen from the top: 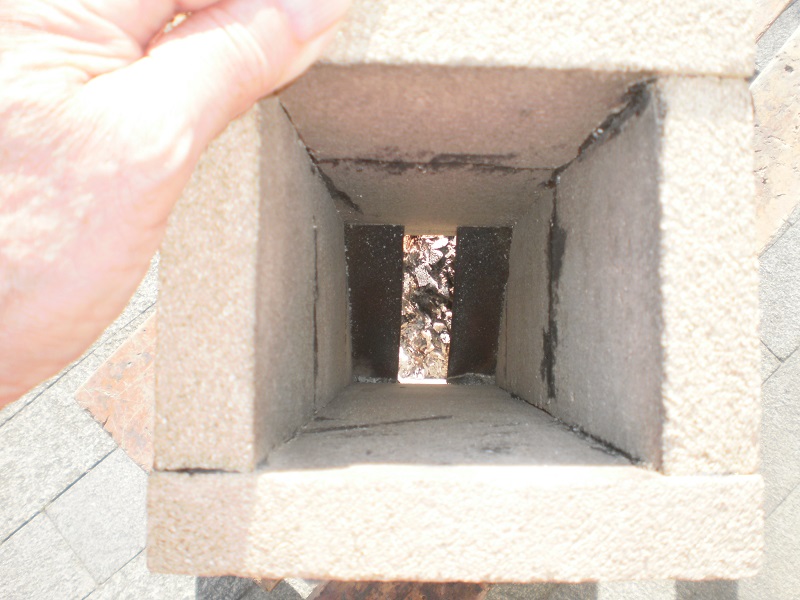 I tried this one with a steel U-shaped plate at the bottom analogue to the Winiarsky specification, so there was some space left under the fuel. This didn't work at all, the thing refused to come up to temperature. Next I took the plate out and built the fire directly on the board. This sort of worked although I wasn't entirely satisfied with it. Totally against my idea of making one change at the time I made a double bend in the riser, restricted the port to 50% and added a small hole to mimic a p-channel, all in one go. This changed the behaviour of the core to such an extent that it looked like I produced a proof of concept. This could be viewed as a variant of the Winiarsky rocket cookstove, although I am unsure at this time about how frugal it is on fuel. 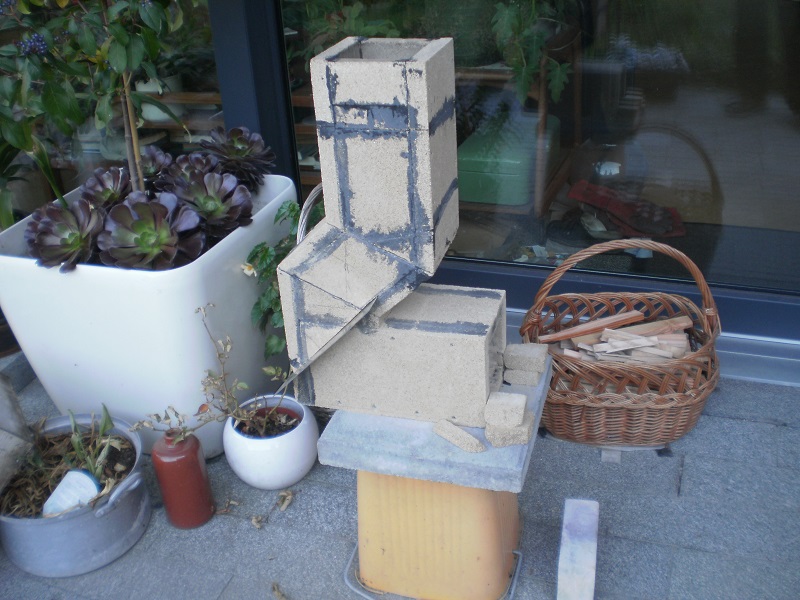 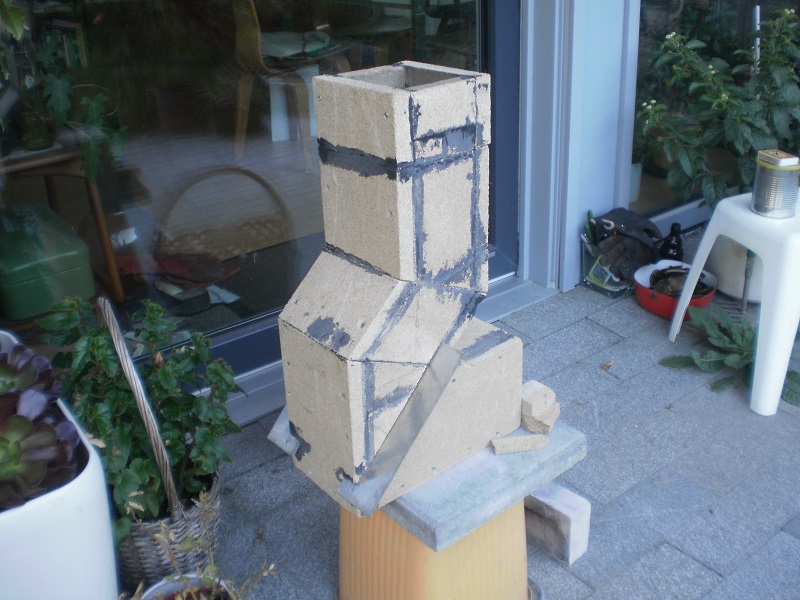 Seen from the front, inside the horizontal firebox: 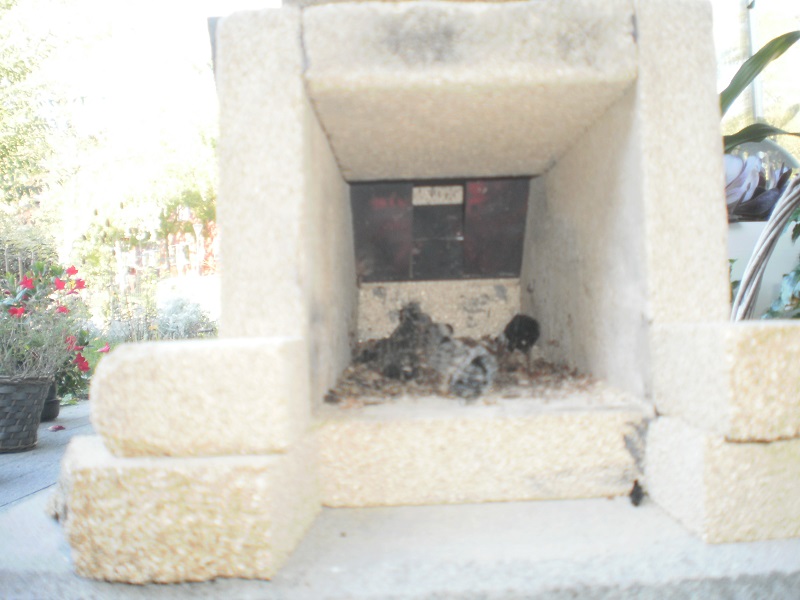 And a video of the first full burn, no sound, sorry: As can be seen in the video there's no smoke produced, the exhaust gases should be tested to know whether it is an enhancement or not. There's more to write about it, but has to wait until tonight or tomorrow.
|
|
|
Post by AlexHarpin on Jan 19, 2017 6:59:35 GMT -8
Awesome!!
|
|
|
Post by wiscojames on Jan 19, 2017 8:28:07 GMT -8
Holy smokes - that's turbulence! Good to see that you are still tinkering. Inspiration for all pyrophiles.
|
|
|
Post by Vortex on Jan 20, 2017 2:20:03 GMT -8
I like the 45 degree port and U-bend. I recon that could be used in a cooktop stove if the exit out of the bend fed under a hotplate.
|
|
|
Post by peterberg on Jan 20, 2017 2:44:15 GMT -8
I like the 45 degree port and U-bend. I recon that could be used in a cooktop stove if the exit out of the bend fed under a hotplate. The goal was a short and low core, specifically intended to serve in a cookstove or similar application, yes.
|
|
|
Post by peterberg on Jan 20, 2017 3:33:48 GMT -8
At this point (October) I decided to build a full-sized experiment, a 120 mm (4.72") system largely following the proportions of the straight batch box core. To this end I ordered some extra light refractory castable from Gouda refractories, Golite 135. This is a 1350º C (2460º F) specced material, density 1400 kg/m³ (87.4 lbs/cu.ft.). Two molds were made, a left and right half of the whole core, out of extruded styrofoam plate with the parts glued in a plywood box. 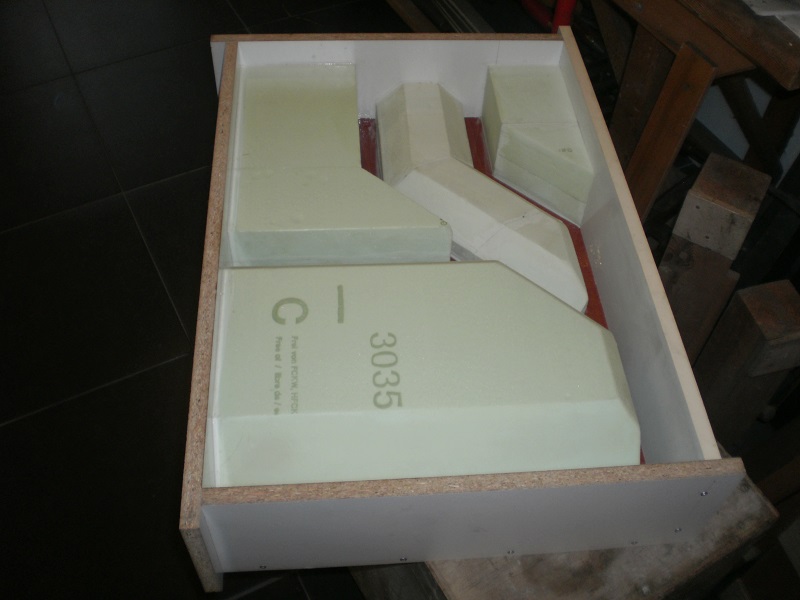 I choose to cast it together with the short riser (even shorter than the proof of concept) since the material was higher specced and more insulative. 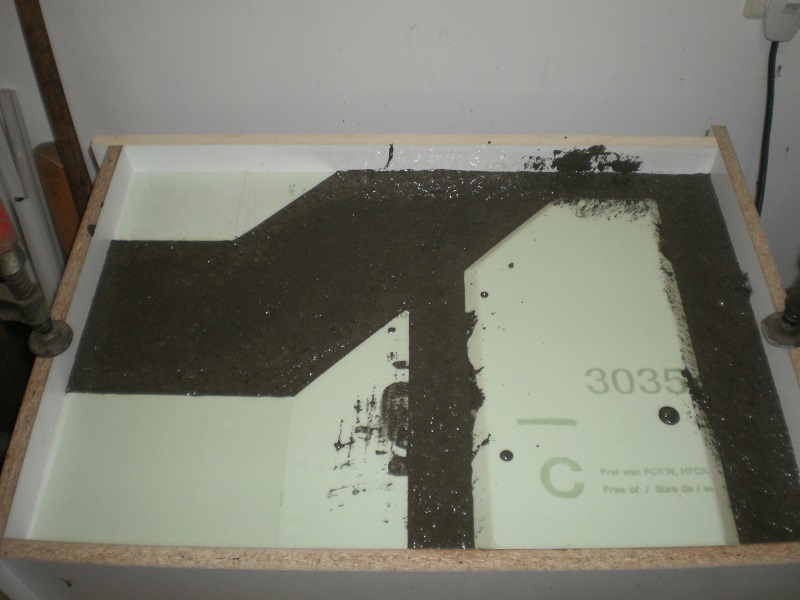 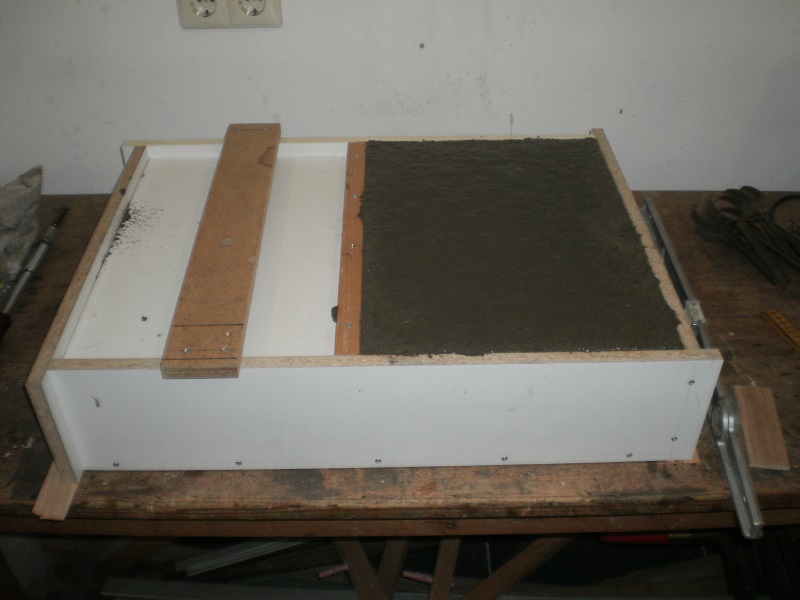 Incidentally, I sold all my 30 year old machines in one go the month before. And bought a Festool shop vac and a DeWalt DWE7491 table saw, that last one being the only one-phase machine capable of cutting 2" material under 45 degrees. A pleasure to use modern tools, the shop vac makes life much easier. 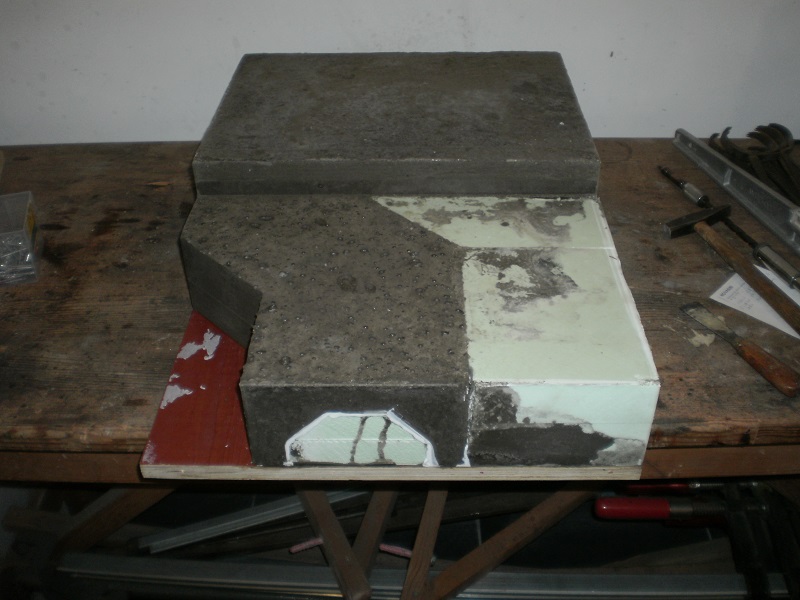 Demolding means the foam has to be cut out, destroying all that time-consuming work. 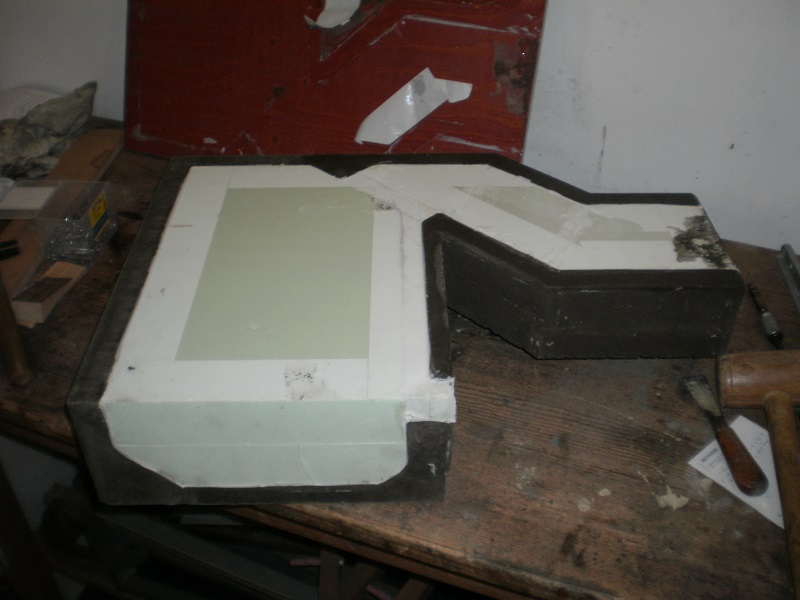 The end result of the right-sided half. 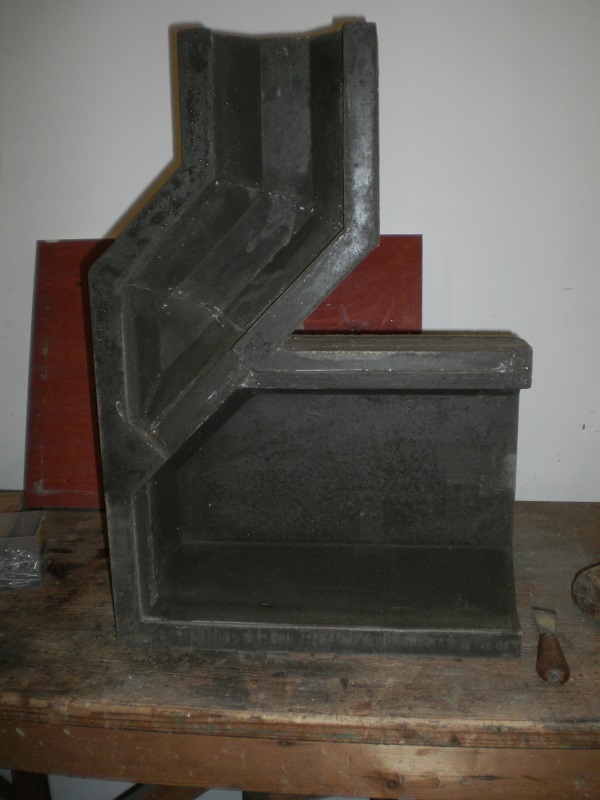 Both the castings were placed near the living room heater and left there to dry out for ten days. The colour is already much lighter now! 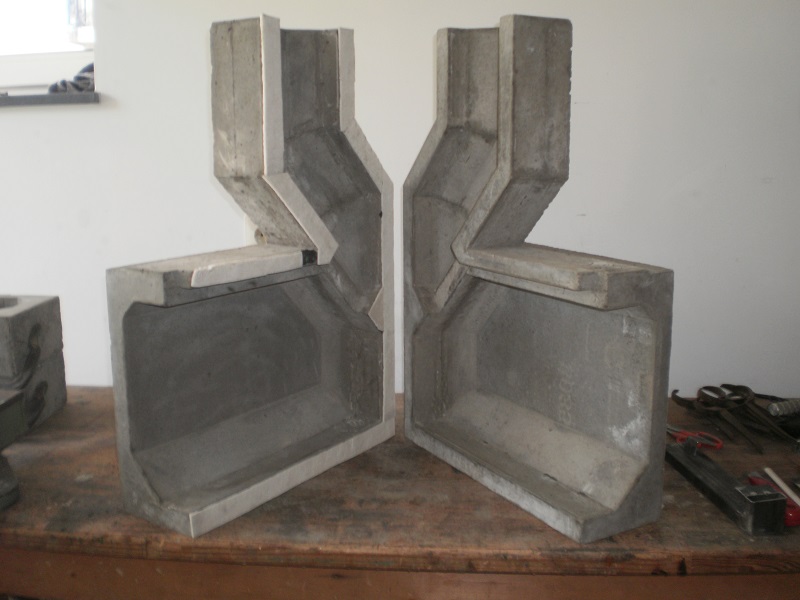 I used a standard steel rectangle duct of 50x20x2 mm (1.97" x 0.787" x 0.0787") to produce the secundary p-channel which was mounted in the ceiling of the firebox so it could feed directly into the port. 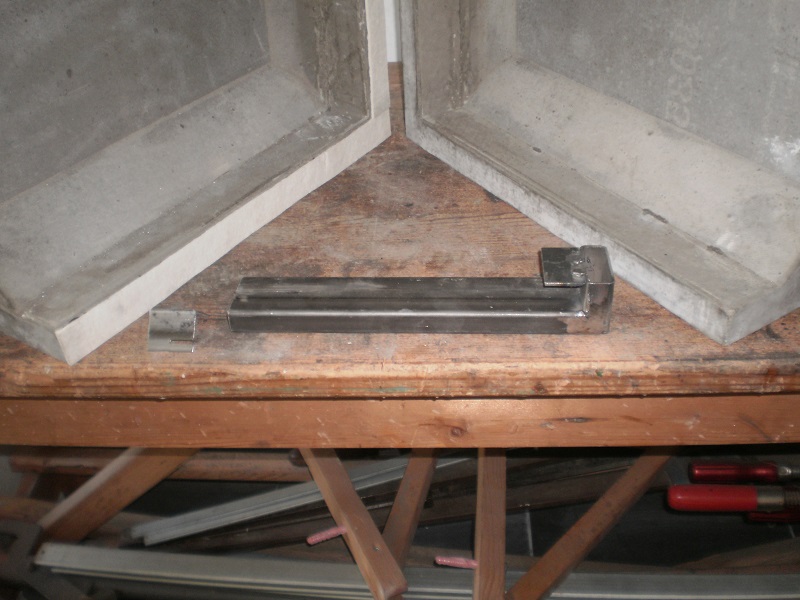 There's a slit in the top of the duct, at the port end, and a slit in that small angled piece in opposite direction. So it can be glided in position and hangs without tension. 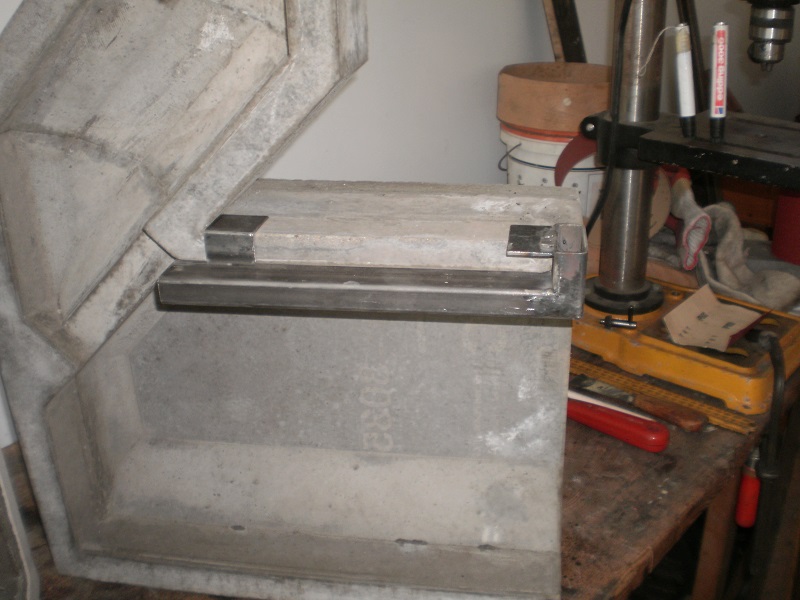 Of course there's more to tell, I'm working on the next article tonight.
|
|
|
Post by pinhead on Jan 20, 2017 5:41:42 GMT -8
Wow, that's some impressive casting work!
|
|
|
Post by peterberg on Jan 20, 2017 7:31:43 GMT -8
Didn't I tell here I worked as a mold maker long ago? And my first real refractory castings are dating back as far as 1982. I had lots of time to think about this sort of stuff.
|
|
|
Post by peterberg on Jan 20, 2017 9:35:07 GMT -8
The core has been assembled outside on the pavement and tested. The results seemed to be very good, although it had the tendency to go into thermal runaway mode almost every time I fired it. Placing the primary air opening at different heights and sizes didn't mitigate this behaviour, most of the time. Actually, it looked like a simple box stove venting straight into a very good chimney stack. 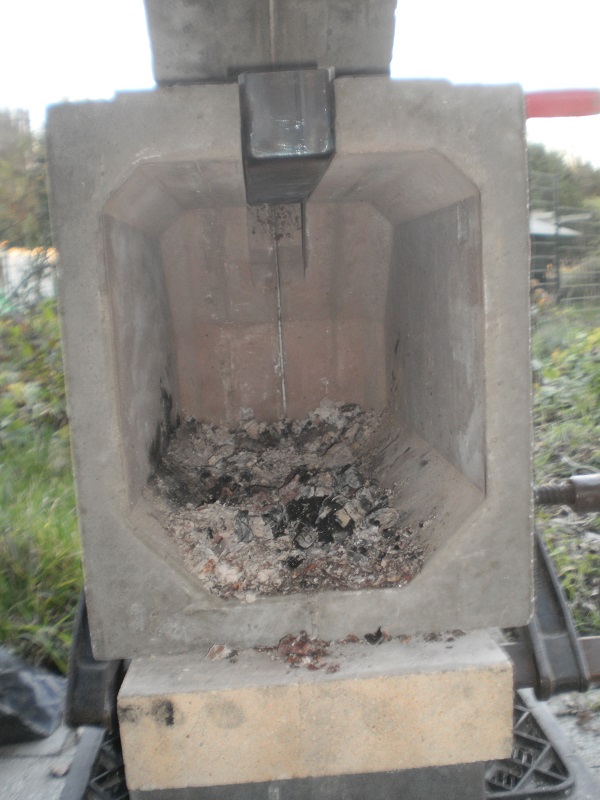 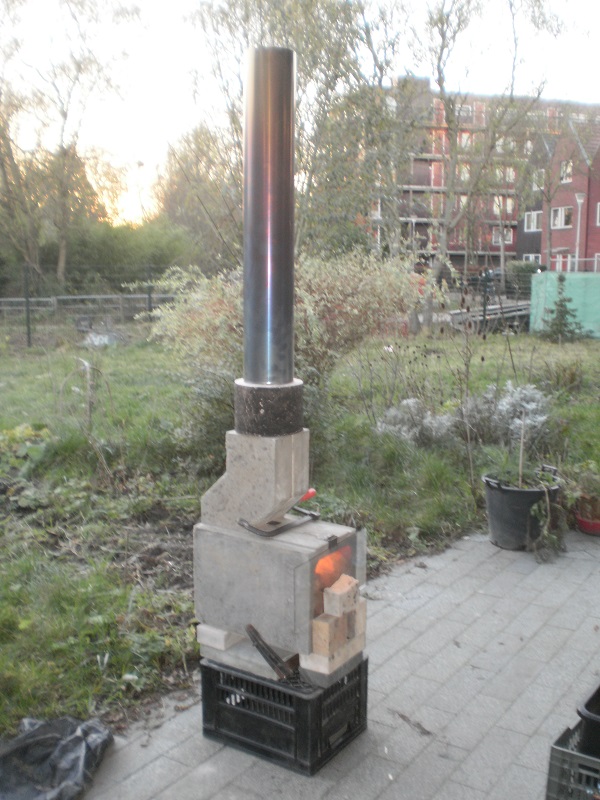 The firebox seemed to react to the restricted port as if there was no restriction at all. Rather the contrary, the suction provided by the port switched the burn in 5th gear within 10 minutes, starting from cold. But still, it burned smokeless without a problem so the afterburner was working, without doubt. Such a setup can't be used to test the thing with an analizer so I planned having two 200 liter (55 gallon) barrels stripped of paint and stacked to function as a bell with the core inside it. Comparing it to a straight standard core, 3.3 m² (35.5 sq. ft.) of ISA should be enough to extract enough heat to get the exhaust temp low enough for measuring. More tomorrow morning(ish).
|
|
Ralf
New Member
Posts: 42
|
Post by Ralf on Jan 20, 2017 14:30:36 GMT -8
Hello Peter,
could you please explain "thermal runaway mode" ?
And thanks for sharing this super ineresting development here !
|
|
|
Post by satamax on Jan 20, 2017 17:25:47 GMT -8
Ralf, thermal runaway, is too much fuel burning at once. Way too much. So much that there is smokey flames comming out of the heat riser.
|
|
|
Post by DCish on Jan 20, 2017 19:16:30 GMT -8
Well! That geometry demonstrates that the critical element for the double ram's horn is a 90 degree transition following the port. If a 50% port upwards at a 45 degree angle can work, a 50% port out the side at half-height should work too. Tonight I did a very crude dry stacked mock-up with the walker core variation I'm playing with out in the yard. It ran like a champ - double ram's horn coming right back toward the front of the stove! I'll try to get a video up over on my Walker Core Variation thread.
|
|
|
Post by keithturtle on Jan 20, 2017 19:26:50 GMT -8
Outstanding work Peter. Thank you for sharing
Turtle
|
|
|
Post by peterberg on Jan 21, 2017 7:26:25 GMT -8
Those two barrels were obtained from a firm quite near me, a few kilometers/miles away. They leach painted furniture in order to get the paint off. Their chemicals are delivered in barrels which are scrap material for them once empty. On my requiest, they used those chemicals to strip the paint off two barrels and had the top of one and the other the bottom cut out. So I was able to buy two bare steel barrels, no burning out, toxic clouds and chances of quarrel with the neighbours. One barrel (the one with the top cut out) I used as the base, with a round hole for the exhaust and a rectangle for the core cut out. 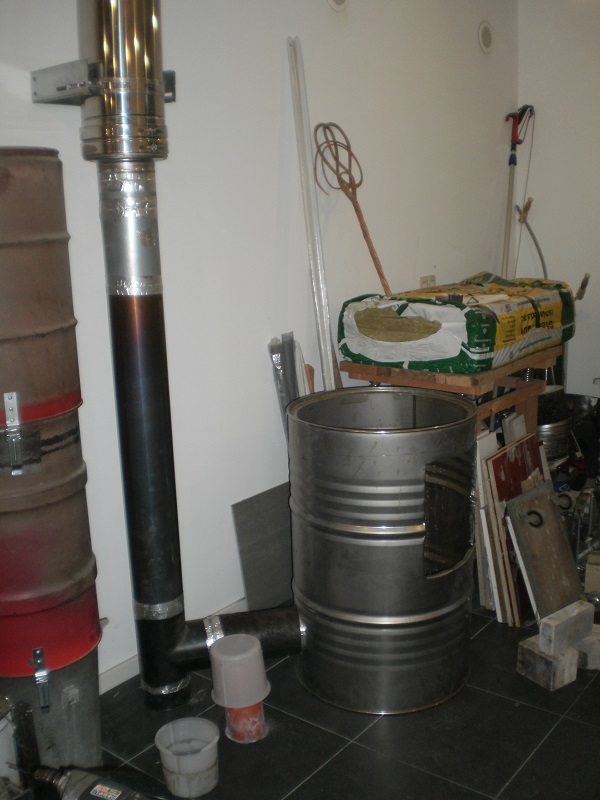 I placed some firebricks on end inside the barrel all around the perimeter in order to be able to place a simple support frame on top. As can be seen, the flanges are a little bit untidy, due to the steel being fairly thin. 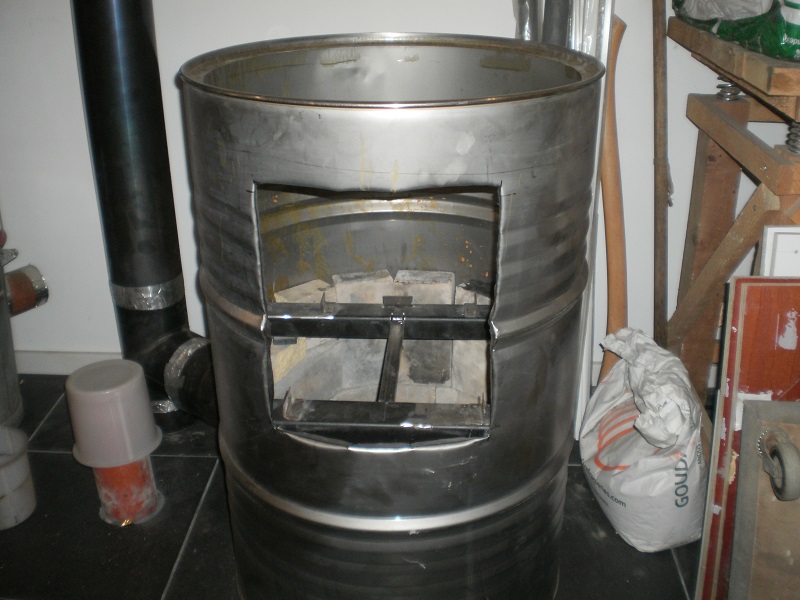 Later on, I replaced the bricks by some steel profiles to hold the frame in position so there wouldn't be any restriction around the core. The core itself was placed on a strip of superwool on the flange and stuffed with the same all around to make it airtight. Because the fibres of that wool are irritating I used good quality aluminum tape to seal it off. 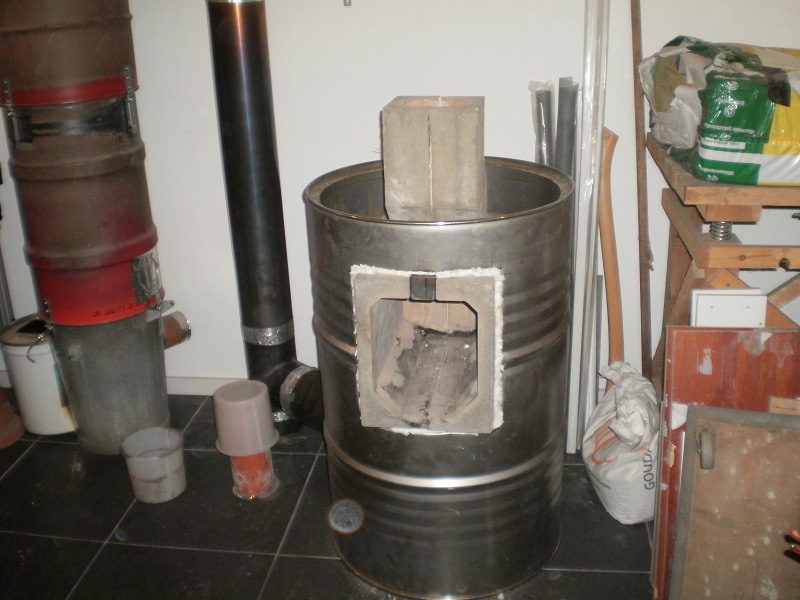 The second barrel on top and there's my experimental mass-less heater. As can be seen, the steel is still bare, I think it looked wonderful. 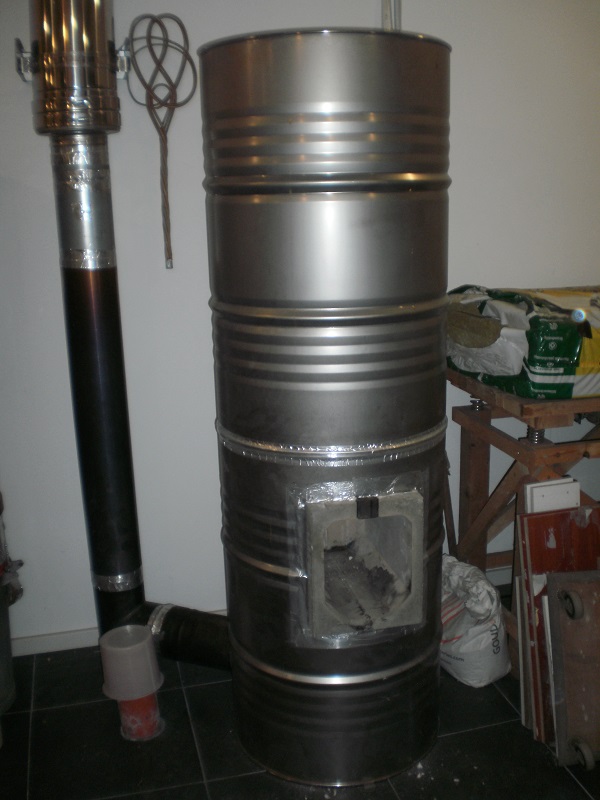 After a couple of burns, the color changed dramatically. There's even twice as much of the surface colored now as compared to the picture. 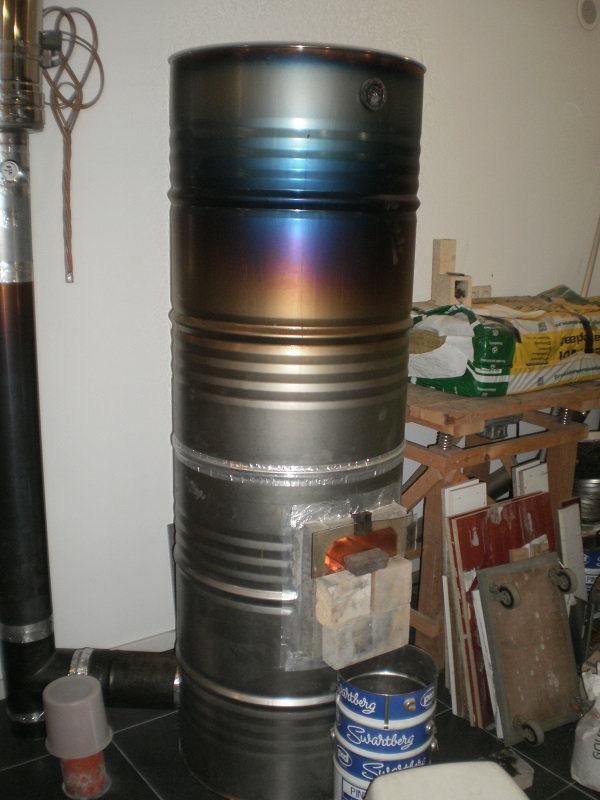 As I said before, I calculated the bell as if it the core was as powerful as the straight batch box core. Boy, was I wrong! The thing was far more powerful than anticipated because of that tendency to go into thermal overdrive. I had to reduce the volume of the firebox with bricks in order to get the fire elevated high enough, running half portions of fuel only. Still, the end temperature happened to be far too high most of the time, in the range of 180º to 220º C (350º to 428º F). The Testo was sometimes very happy with it but it proved to be very difficult to pull the handbrake all the time. Here are two videos, both taken during the same run at the height of the burn. The front inlet was very restricted but still the thing was running like no other. Now it is clear why I opted to have the bottom of the upper barrel cut out. This way, the bung holes were still at the top so I would be able to have a quick peek and shoot a video. At the time, I didn't get as far as producing a door of some sorts. The whole of the testing was done using a hotchpotch of bricks, a piece of Robax glass, steel tubing and cobbled together air inlets. I tried different configurations, the main air inlet higher up, even at the top, or low with a barrier behind to divert the stream up but to no avail. At some point I welded another p-channel, 50x30x2 mm (1.97" x 1.18" x 0.0787), only minimal tweaking of the core was necessary to have it fitted. 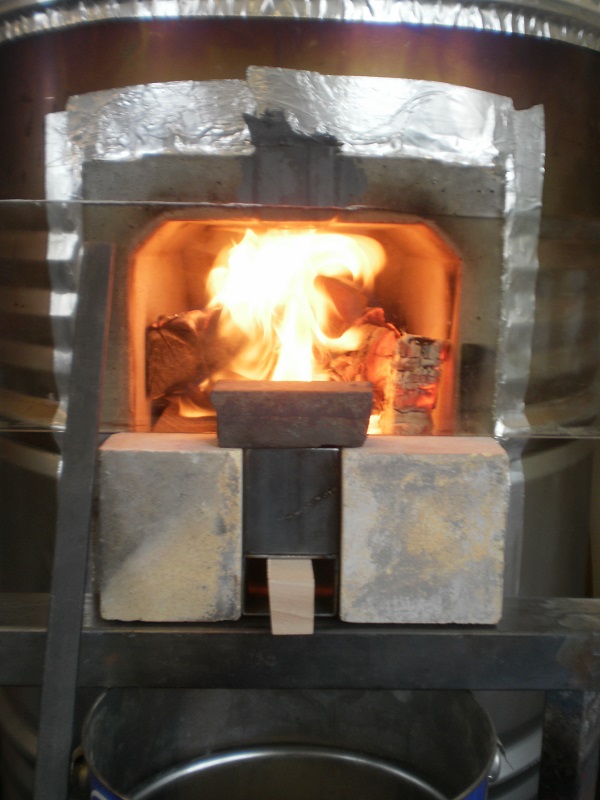 As a result, the core seemed to behave a little bit better, the Testo registered higher excess air and CO was in a range where it would be certainly acceptable. More about the test runs tomorrow.
|
|
|
Post by Vortex on Jan 21, 2017 11:08:31 GMT -8
Nice temper colors you're getting on the barrel.
Have you tried firing it with larger pieces of wood? I find that solves the thermal runaway problem in the vortex stove.
|
|