|
Post by stephenson1 on Jan 10, 2014 6:12:57 GMT -8
 Icarus, you asked for some more details. Unfortunately I was so busy building I neglected to take many detail photos prior to cobbing. I (sort of) diagrammed one of my photos for what it's worth. BTW, so far I can't personally recommend drawing air through the ash pit, as it hasn't worked yet for me. Radek has what looks to me like a really nice solution with his build drawing air through the side of the small barrel above the feed tube. Good luck. Mark
|
|
|
Post by akaleather on Jan 11, 2014 22:47:51 GMT -8
Mark, thank you for creating this thread and video. It is a very original idea. Are all of the fire brick used in your build the thin split bricks or did you use full size bricks as well?
|
|
|
Post by icarus on Jan 12, 2014 18:18:30 GMT -8
Mark, Thanks much for the pic.
|
|
jacob
New Member
Posts: 14
|
Post by jacob on Jan 13, 2014 23:20:01 GMT -8
Very impressive. Excellent idea with the cinder blocks. May be prone to cracking and putting C0 in the air though. Perhaps it's better not to sit on it, and just use it to store heat.
You would not want an adult standing on it, or even a child jumping u and down on it.
Plus if you leave the blocks exposed, you could use a detector to find C0 leaks, and periodically mend them with KAO caulking.
I have a couple questions. I love the 16 gallon barrel. That is what I will be going with.
What is the effective inside diameter of the riser?
is it the same effective diameter as your intake and burn tunnel? ( 4 inches ), or is it larger?
I am wondering if slightly larger riser diameters create better draft.
Also do you have any idea how the dynamics of this system would change if I wanted to have a 6 inch burn tunnel, and riser? So if everything was identical except inner diameter of system was 6 inches what would happen?
separate question entirely:
I am also thinking of going horizontal feed. I would like to make a really long feed tunnel to put lots of fuel in.
Any idea what happens to a system if you are running horizontal and make the feed tube longer? Does the riser need to get longer to compensate?
Or does it not make a difference. Doesn't seem like horizontal would compete with the chimney effect of the riser much.
Great job on the RMH!
: )
|
|
|
Post by pinhead on Jan 14, 2014 6:21:50 GMT -8
I am also thinking of going horizontal feed. I would like to make a really long feed tunnel to put lots of fuel in. Any idea what happens to a system if you are running horizontal and make the feed tube longer? Does the riser need to get longer to compensate? Or does it not make a difference. Doesn't seem like horizontal would compete with the chimney effect of the riser much. Great job on the RMH! : ) Sounds to me like you need to look into a Peterberg Batch Box.
|
|
|
Post by stephenson1 on Jan 15, 2014 6:34:27 GMT -8
I used a mix of full and thin hard fire bricks for the core. I'm attaching more pics to give offer more details. Now that it's mostly cobbed over I don't recall specific choices I made. My goal was to use thin brick wherever practical so that I could keep the mass of the core down. On the first page of this thread I posted notes about specific dimensions, particular CSA's can be (roughly) calculated from those. My goal was to increase the csa incrementally to insure that I didn't accidentally restrict the flow. As an example; the holes in the cinder blocks are probably more than twice the csa of the feed. I chose to do that because I'm pretty new to these things and feel it is better to control things at the source of combustion. As far as cinder blocks and heat stress; my sense is that the temps at the atrium (aka manifold) where the hot gasses first meet the concrete are low enough that there is no real risk of making the blocks fragile, but I haven't taken readings and don't know what concrete can stand. Regarding noxious gasses leaking through the concrete; the permanent draw created by tying into the chimney seems to insure that there is no pressure anywhere in the system, so I can't see that being an issue. On the other hand, I installed a CO monitor and got a dedicated fire extinguisher for that space just to be safe. A batch feed with rmh seems to have been done very successfully by Mathew Walker, and frankly, he and several others can speak about these things with more authority than me. Good luck, and definitely keep experimenting (cautiously). -Mark
|
|
|
Post by stephenson1 on Jan 15, 2014 6:37:02 GMT -8
One more pic with more detail of the atrium (manifild). BTW, a wet saw is a HUGE advantage to building what you actually want. -Mark Attachments:
|
|
|
Post by patamos on Jan 15, 2014 9:55:08 GMT -8
Thanks for showing this Stephenson,
I am beginning something similar with a more open bell using concrete pavers for the roof of an open chamber. Supported by brick posts under. I am fairly new to stove building but have been natural building houses for many years now. One way to strengthen the top deck of your mass/flue chamber is to make a browncoat plaster (cob with well chopped straw) wet enough to spread (more like wiggle and drag) with a wooden or magnesium float. Place 1" at a time and then embed loose weave burlap that has been presoaked in clay slip. Cob over top of that with another 1/2" or so and you will have an organic mesh sandwich. Used coffee sacks are good for this, but go for the thinner looser weave. You could also use fiberglass mesh in 1/4" size. This is a good way to increase tensile strength and prevent cracking. The more cob-mesh-cob-mesh-cob... layers you embed the stronger and more air tight it becomes The lime will serve better as a thinner hard finish plaster
well being
pat
|
|
|
Post by patamos on Jan 15, 2014 21:32:54 GMT -8
Hi Y'all I happened to be reinforcing a bell pier today and therein applying the technique that i wrote about this morning, so thought i'd offer some pics.  First clay slip the surface, then trowel on fairly wet cob with short (1/2" or so) straw fibre. Best way to make it that short is with a top-feed leaf shredder/mulcher that fits over a garbage can. MIght be able to source it in bags or barrels from livestock suppliers. For your application i'd recommend laying on at least 3/4" thick to start. This will distance the mesh from any micro fissures in the cob as it dries  Then spread fiberglass mesh across and rub it in with your palm. Best to rub in one direction so it doesn't wrinkle as it beds in 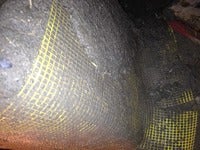 Then apply another layer of cob. For the first mesh layer i'd go with fiberglass cuz it will withstand higher heat than burlap before burning out This may be all the reinforcement you need. But another similar sandwich with burlap on top of that will make it bomber. btw. burlap is way easier to work with as it changes shape and bed in way easier. I have a few longer stories of how i gained faith in this approach... but for now am just wanting to share back into this forum that has been helping me out so much. well being pat  Attachments:

|
|
|
Post by stephenson1 on Jan 16, 2014 4:41:51 GMT -8
Thanks for sharing that Pat. I can well imagine how strong it will be with all of those layers. For me that process is down the road when I settle into my dream house. My little heater is really a temporary construction. It's meant as emergency backup only, and I'll have to remove it one day before I move on. I have no plans to do the kind of excellent work you are showing just yet, but it'll be great to have it as a reference.
I'm hoping this forum will maintain all this great stuff indefinitely! -Mark
|
|